1.1.Немного из истории создания системы ТРМ, или Почему о ней так долго молчали японцы
Теперь уже общеизвестно, что система «Общего производительного обслуживания оборудования», т.е. система ТРМ, родом из Японии, но, как не менее широко известно, японцы – талантливые копиисты, которые умеют не только быстро заимствовать, но и развивать все полезное, что находят в чужой теории или практике.
Так случилось на этот раз и с системой ТРМ. Ее прообраз – система PM (Preventive Maintenance, а затем и Productive Maintenance, т.е. предупредительное/производительное обслуживание) пришла в Японию из США в послевоенные годы вместе со многими методами и приемами западного менеджмента под воздействием американской оккупационной администрации. В этот период политика США была направлена на то, чтобы превратить поверженного врага в сильного, но управляемого союзника. Судить, насколько и в чем удался этот замысел, предоставим политикам, а наша задача – разобраться сначала в истоках ТРМ.
Производственники старшего и среднего поколения, вероятно, помнят аббревиатуру ППР (планово-предупредительный ремонт), широко использовавшуюся на отечественных предприятиях, также как и практику этого ремонта – хотя и не всегда удачную, но сыгравшую выдающуюся роль в развитии промышленности СССР.
Планово-предупредительный ремонт зародился в 1923-1928 гг. на Выксунском и Кулебакском металлургических заводах и получил развитие в 1928—1932 гг. на Московском станкостроительном заводе имени С.Орджоникидзе. Дорогостоящее импортное оборудование, приобретаемое для индустриализации страны, необходимо было не только эффективно использовать, а работало оно тогда зачастую в три смены, но и как можно дольше сохранять в работоспособном состоянии и с поддержанием его качественных характеристик.
В эти годы и сформировались основные концептуальные принципы отечественной системы ППР:
- периодические ремонты по количеству отработанных оборудованием часов (определение срока службы узлов и агрегатов до их ремонта или замены);
- планирование ремонтных работ и изготовления запасных частей для их проведения (понятие «синхронизация» тогда не использовалось, но запчасти должны быть готовы или, что реже, приобретены к плановому сроку начала ремонта);
- проведение периодических осмотров оборудования и выполнение послеосмотровых ремонтов по их результатам (в будущем – ремонты по состоянию);
- планирование и реализация периодически повторяющихся ремонтных циклов (малые, средние, капитальные ремонты).
В конце 30-х гг. из двух основных подходов: 1) ремонты по времени эксплуатации и 2) ремонты по состоянию оборудования, оцениваемому в ходе осмотров, и сформировалась отечественная система ПППР или ППР – планово-предупредительных периодических или планово-профилактических ремонтов оборудования.
Будучи официально принятым условием успешного развития индустриализации, эта система была быстро подкреплена нормативами на проведение ремонтов и организацией специальных ремонтных подразделений (цехов, участков) на заводах. Для них выделялось до 10% производственных мощностей предприятия.
Широкое применение системы ППР стало одним из решающих факторов обеспечения жизнеспособности нашей промышленности в годы Великой Отечественной войны. Несмотря на высокую, практически предельную, загрузку оборудования, уход на фронт квалифицированных кадров, работу в условиях эвакуации, оборудование удалось сохранить и выпускать на нем оружие победы! Конечно, экстремальные условия внесли коррективы в нормативы ремонтных циклов и продолжительность ремонтов, но, тем не менее, они проводились, и благодаря ППР оборудование поддерживалось в работоспособном состоянии.
История умалчивает о том, была ли наша система ППР заимствована и превратилась в PM (Preventive Maintenance, а затем и Productive Maintenance) или же сформировалась самостоятельно в послевоенные годы в США и получила там распространение. Но мы должны осознавать, что у японской системы ТРМ, как минимум, – два «родителя», но, как бывает и в жизни, ребенок не всегда знает обоих из них.
Итак, вернемся в Японию начала 50-х. В этот период страна, потерпевшая поражение и разрушенная войной, стремительно возвращалась к жизни, впитывая, заимствуя и используя все то из западного производственного опыта, что было закрыто от нее в предвоенные десятилетия, когда даже изучение английского языка (языка потенциального врага) могло быть приравнено к предательству с вытекающими последствиями. Образ процветающей послевоенной Америки, ее уровень благосостояния и образ жизни стали путеводной звездой для многих японцев, несколько десятков тысяч которых американская оккупационная администрация сознательно направляла в США на экскурсии и стажировки.
Организованный в этот период в Японии пятидневный семинар выдающегося американского ученого и практика в области статистики и управления доктора Эдварда Деминга, который раскрыл японским руководителям бизнеса преимущества использования семи простых статистических инструментов для повышения качества продукции, произвел переворот в сознании японских менеджеров. Руководители, а за ними и рядовые рабочие стали упорно осваивать и применять на практике эти инструменты. Для изучения и применения статистических методов на предприятиях создавались кружки качества – прообраз будущих Рабочих групп (из рабочих), реализующих на своих рабочих местах многие из инструментов Бережливого производства.
Применение статистических инструментов приняло масштаб общенациональной кампании, а Э.Деминг стал непререкаемым авторитетом и гуру в развитии экономики, в т.ч. и в гуманистической составляющей системы менеджмента, не понятой и не принятой поначалу в США. Институт Э. Деминга, ежегодные конкурсы и премии за успехи в области качества во многих номинациях, медали Э. Деминга стали частью национальной промышленной культуры Японии.
С не меньшим рвением стали использоваться и инструменты PM (Preventive/ Productive Maintenance), тем более что растущее промышленное производство втягивало в себя все больше сельского населения, весьма далекого от работы на оборудовании.
Для изучения и распространения лучшего опыта технического обслуживания оборудования был создан Японский институт производственного технического обслуживания (JIPM); проводились ежегодные конкурсы; вручались почетные знаки, дипломы и премии за достижения в области РМ.
Традиционная американская концепция PM (предупредительное /производительное обслуживание) предполагала четкое разделение обязанностей в работе с оборудованием между операторами и ремонтным персоналом. Коротко это разделение можно сформулировать одной фразой: «Оператор работает на оборудовании, а технический персонал его ремонтирует». Практическая реализация этого принципа зачастую приводила к взаимному неприятию этих двух категорий персонала, выражавшемуся словами: «Они не умеют работать на оборудовании и ломают его, а мы чиним» или «Нам работать надо, а они починить не могут».
Примерно такой же, если судить по комиксам из японского издания (рис. 1.1.1 и 1.1.2), была ситуация и на японских предприятиях.
Среди компаний, применявших принципы РМ, была и «Nippon Denso» – поставщик автокомпонентов для «Тойоты». В результате автоматизации производства и использования нового оборудования в 60-е годы в компании возникла проблема эффективного использования этого сложного оборудования. Увеличение численности вспомогательного персонала (технической службы) приводило к росту затрат, но не давало существенного улучшения ситуации. При этом операторы простаивали во время выполнения работ по ремонту и техническому обслуживанию оборудования.
Найти решение удалось с помощью двух основных принципов.
Во-первых, операторам было вменено в обязанность не только эксплуатировать оборудование, но и осуществлять его текущее техническое обслуживание (см. рис. 1.1.2).
Во-вторых, на основе кружков качества начали создавать группы технического обслуживания и ремонта, которые стали заниматься наиболее важными работами по техническому обслуживанию, что переросло в дальнейшем в систему поддержания в нормальном состоянии всего оборудования компании ее персоналом. Такой подход дал заметный рост эффективности работы оборудования.
В 1971 г. «Nippon Denso» подала заявку в Японский институт PM (JIPM) на присуждение премии за лучшее обслуживание оборудования, но эксперты, проводившие аудит предприятия для подтверждения заявки, обнаружили нечто новое – включенность ВСЕГО производственного персонала в процесс обслуживания и достижение высокой эффективности работы оборудования. Это новое явление в японской промышленности получило название система ТРМ (Total Productive Maintenance) – система «Общего производительного обслуживания оборудования».
Таким образом, с 1971 г. предприятиям, добившимся высоких результатов в обслуживании оборудования с участием всего персонала, вручаются премии ТРМ различных номинаций.
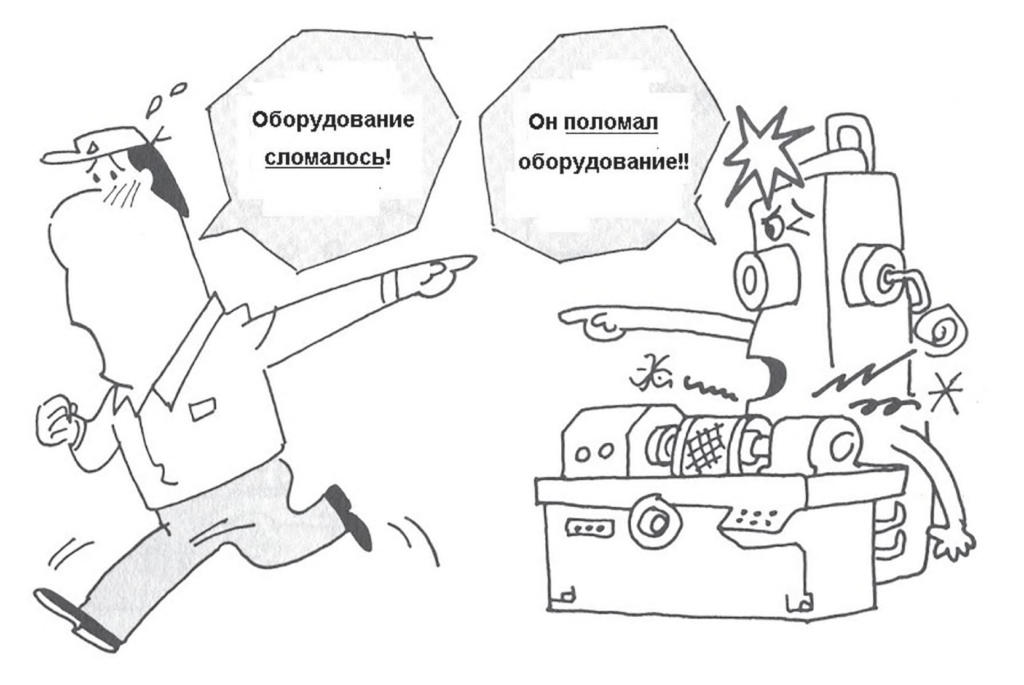
По материалам источника 4, с.50.
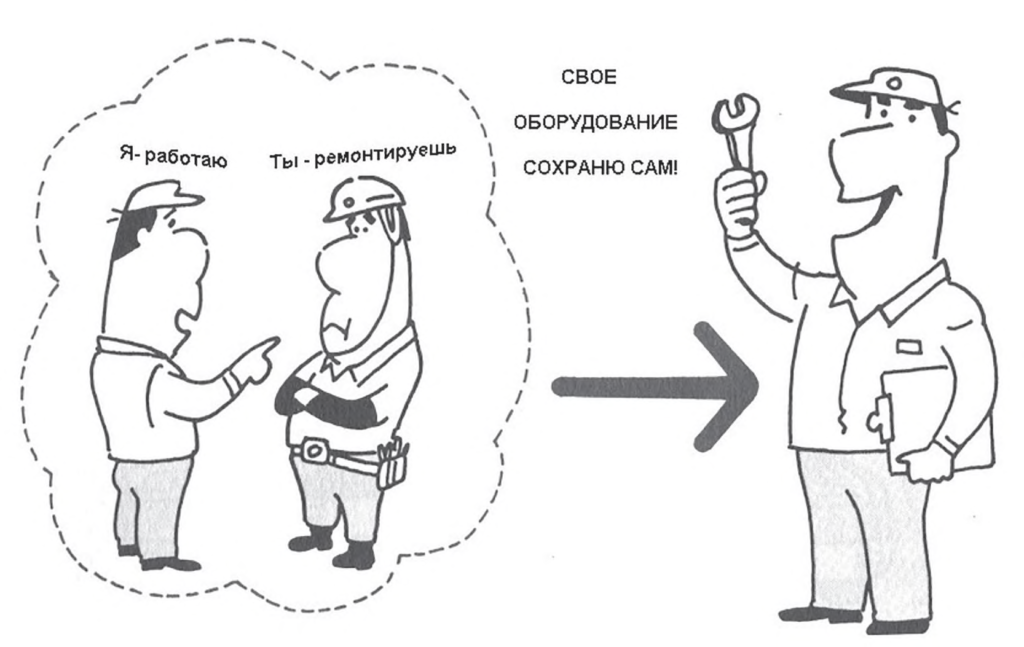
По материалам источника 4, с.54.
Начиная с 1991 г. эта премия стала международной, ее вручают и иностранным компаниям. По данным сайта Японского института производственного технического обслуживания (JIPM), в России премию ТРМ получили:
- Тульский комбинат продуктов питания компании Unilever (2005 г.);
- Чаеразвесочная фабрика компании Unilever, С-Пб. (2006 г.);
- Завод по производству жевательной резинки компании Wm. Wrigley Jr. Company, С-Пб. (2006 и 2008 гг.);
- Фабрика по производству упаковочных материалов компании Tetra Pak, Москва (2010, 2012, 2014, 2017гг.);
- Завод по производству смесителей компании VitrA, Московская обл. (2016 г.).
Описанием системы ТРМ и ее продвижению в мире мы обязаны, в первую очередь, замечательному японскому инженеру и менеджеру Сейичи Накадзиме (рис. 1.1.3) – заместителю председателя Ассоциации «Японский институт производственного технического обслуживания (JIPM)».
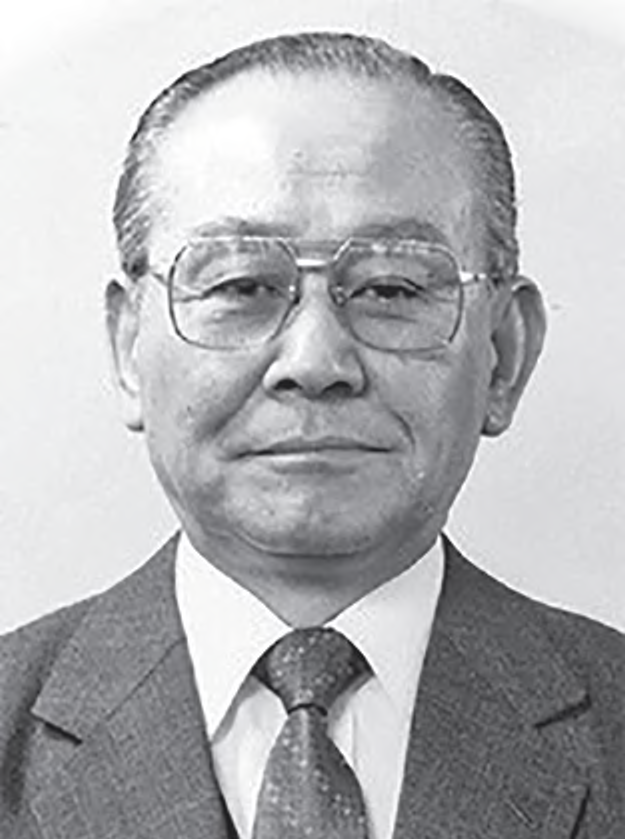
Благодаря таким его публикациям на английском языке, как «Introduction to TPM» (1988) и «TPM Development Program» (1989), система ТРМ стала входить в практику американского, европейского, а затем и российского менеджмента. Мы впервые смогли познакомиться с методиками ТРМ в 1992-1993 гг. в ходе совместной работы с консультантами Японского центра производительности.
Возникает закономерный вопрос, почему система ТРМ, являющаяся составным элементом Производственной системы «Тойоты» (TPS), в течение 18 лет находилась в тени, если не сказать в тайне, и, в отличие от систем TQC/TQM или JIT, публикации о ней практически отсутствовали. Даже такие скрупулезные исследователи феномена «Тойоты», как Вумек, Дж., Джонс, Д., Рус, Д., изучавшие его в 1985-1989 гг., в своей книге «Машина, которая изменила мир». /Пер. с англ./ – Мн.: «Попурри», 2007. – 384 с.), о ней вовсе не упоминают.
Позволим себе высказать несколько гипотез на этот счет:
- Система ТРМ формировалась, вырастала из практики работы японских предприятий, и на ее рост, осмысление, обобщение, описание требовалось время (порядка 10-12 лет).
- Система ТРМ оказалась одним из самых сильных производственных организационно-технических инструментов. Она позволяет достигать при правильном применении почти двукратного роста эффективности использования оборудования. Например, коэффициент общей эффективности оборудования (КОЭ), о котором речь еще впереди, увеличивается с 40-45 до 80-85%, а то и до 90%.
Двукратный рост производительности оборудования практически без капитальных затрат – это мощное конкурентное преимущество, которое не стоит «просто так» отдавать миру, а целесообразно до поры до времени приберечь для себя. Вспомним, что именно в 70-е годы Япония вступила в круг высокоразвитых мировых держав, а в 80-е совершила сокрушительную экспансию на американский автомобильный рынок, захватив 40% его объема продаж. Этот факт и стал предметом исследований и открытия новой промышленной эпохи – эпохи Бережливого производства (сокращенно TPS-Lean: от Toyota Production System – Lean Manufacturing).
И только укрепив свои позиции на мировых рынках и имея запас прочности в части себестоимости продукции, Япония начала постепенно раскрывать карты своего менеджмента. Как мы уже отмечали, первые публикации на английском языке появились в 1988 и 1989 гг. - Система ТРМ – одна из самых сложных и многоплановых в комплексе TPS-Lean. По нашему мнению, ее освоение требует от компании обеспечения таких условий, как:
- готовность первых лиц и менеджмента компании к вложению своих сил и времени в освоение, реализацию и поддержание системы ТРМ;
- наличие проблемной ситуации – необходимости бороться за выживание или укрепление позиции компании на рынке средствами ТРМ;
- высокая сплоченность коллектива, его готовность к новой и непростой работе;
- способность найти и привлечь консультантов, имеющих успешный опыт консультационного сопровождения внедрения ТРМ;
- опыт и положительные результаты в освоении некоторых инструментов Бережливого производства. Например: во внедрении и поддержании системы «Упорядочение/5S», в устранении основных видов потерь, в приобретении навыков использования простых статистических инструментов (рис. 1.1.4 а и 1.1.4 б).
Статистические инструменты решения проблем
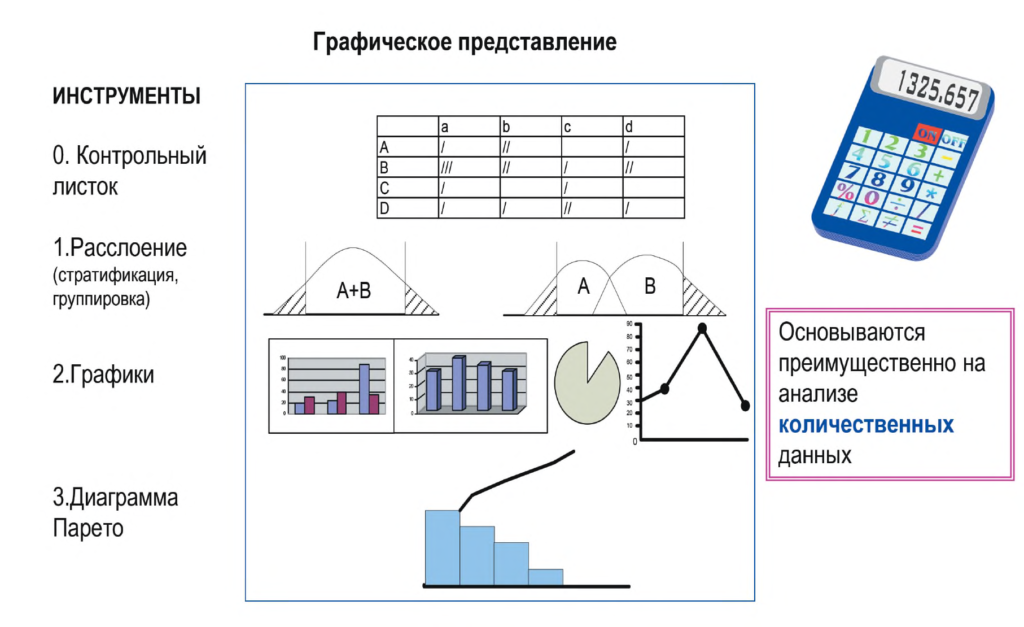
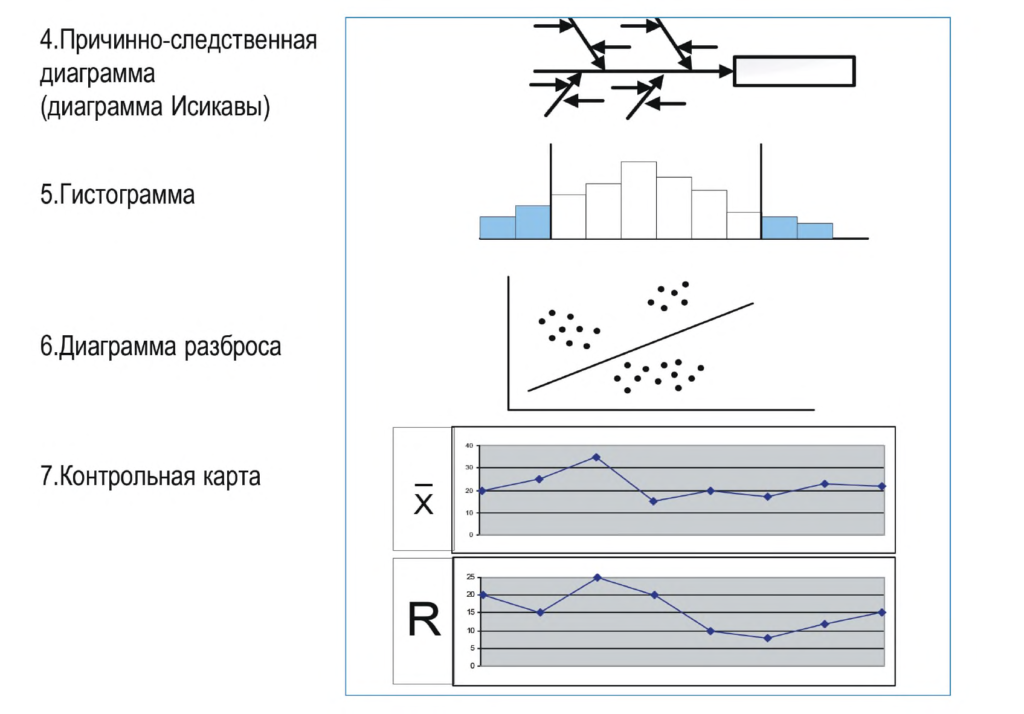
Как вы понимаете, сочетание всех приведенных выше условий является довольно редким случаем, а без этого сочетания, полагаем, даже самая хорошая и детальная методика не принесет предприятию ожидаемых результатов (кроме потерянного времени и разочарования). В своей практике мы неоднократны были свидетелями таких ситуаций, когда приходили на «затоптанное пастбище» бессистемных попыток внедрения ТРМ.
Какая из наших гипотез причин почти 20-летней закрытости системы ТРМ верна, судить вам, уважаемый читатель. Возможно, у вас появятся и свои соображения на этот счет. А теперь давайте приступим к изучению и, надеемся, практическому применению вами системы ТРМ.