Для руководителей основным привлекательным моментом во внедрении системы ТРМ является, конечно, возможность получить высокие результаты в повышении эффективности и укреплении конкурентоспособности своего бизнеса.
В японской системе ТРМ декларируются такие результаты, которые в общем виде выглядят почти фантастически. Это:
- Эффективная эксплуатация и высокий уровень обслуживания оборудования (в пределе «Ноль поломок»).
- Высокий уровень качества (в пределе «Ноль дефектов»).
- Высокий уровень условий труда (в пределе «Ноль травм»).
- Разработка новых продуктов под лозунгами: «Просто для производства» и «Удобно в эксплуатации и обслуживании».
- Рациональное использование всех видов ресурсов (в пределе «Ноль потерь»).
- Формирование нового производственного поведения персонала.
Если использовать сухой язык количественных показателей, то традиционно в японском менеджменте эффекты от внедрения ТРМ (рис. 1.2.1) рассматриваются по шести направлениям:
- P (Productivity) – Производительность
- Q (Quality) – Качество
- C (Cost) – Затраты, стоимость производства
- D (Delivery) – Дисциплина поставок (или своевременность поставок, поставка в короткие сроки)
- S (Safety) – Безопасность (в узком смысле – персонала, в широком смысле – еще и охрана окружающей среды)
- M (Moral) – Мораль, или высокая сознательность, ответственность и дисциплинированность персонала.
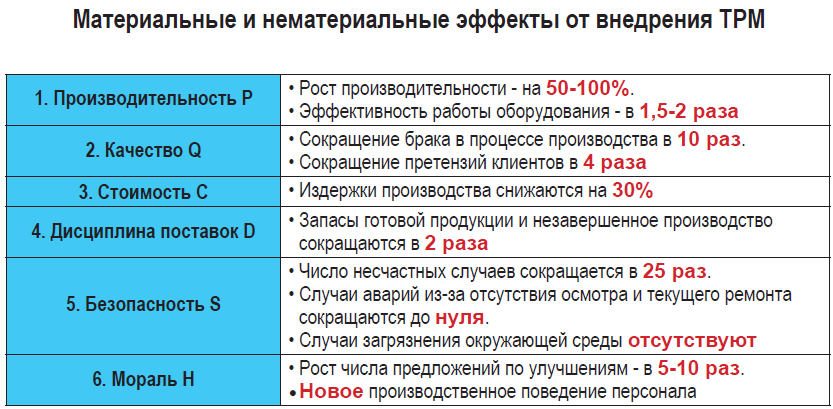
Источник: 12, р. 18.
Кроме того, в материалах JIPM (источник 12, р.18) отмечается также группа так называемых качественных, нематериальных результатов. Это:
- Деятельность по самостоятельному обслуживанию оборудования операторами становится частью производственного поведения персонала и выполняется согласно регламентам (стандартам) обслуживания без дополнительного контроля со стороны руководства.
- Чистые и эстетично выглядящие производственные помещения и оборудование создают позитивную атмосферу в производстве, улучшают настроение персонала, что косвенно отражается на повышении производительности и улучшении качества.
- Внешний вид чистого производства и удовлетворенных сотрудников позитивно влияет на имидж компании, внушает доверие и уважение посещающим его клиентам и партнерам.
Сразу же оговоримся, что далеко не на каждом предприятии, даже японском, можно одновременно получить все перечисленные выше результаты и в указанном масштабе. Это, безусловно, – лучшие примеры, да еще и с учетом того, каков был стартовый уровень предприятий, относительно которого проводится сравнение результатов. Плюс следует принять во внимание и целевую ориентацию внедрения – что было наиболее важным для стратегии компании при внедрении ТРМ (например, производительность оборудования, качество, себестоимость продукции или производственный травматизм). Тем не менее, можем с уверенностью сказать, что в значительной степени подобные результаты реально достижимы.
Предвидим скептические возражения: «Да это результаты, полученные в Японии, а в наших условиях да с нашим персоналом такое невозможно!». Согласимся, что это действительно не просто. Да и в Японии к таким результатам приходят через 3-5, а то и больше лет после начала внедрения.
Для скептиков приведем примеры, являющиеся результатами наших консультационных проектов по внедрению ТРМ на отечественных (преимущественно) предприятиях. Результаты эти в большинстве случаев были подтверждены службами предприятий (экономистами и финансистами, техническими подразделениями) и опубликованы в СМИ.
В этом разделе мы приводим только факты, не останавливаясь на содержании проектов и решениях, которые привели к получению результатов. (Подробно эти проекты будут рассмотрены в последующих разделах книги).
Для понимания многих из приведенных ниже примеров остановимся коротко на основном показателе, оцениваемом и учитываемом в системе ТРМ для анализа проблем и динамики изменений в эффективности работы оборудования. Это – КОЭ, т.е. коэффициент общей эффективности оборудования, по-английски ОЕЕ (Overall Equipment Effectiveness) или OPE (Overall Process Effectiveness).
КОЭ представляет собой произведение трех коэффициентов: К1 х К2 х К3,
где:
К1 – коэффициент использования планового фонда времени, или коэффициент доступности оборудования. Это – время, когда оборудование может работать, т.е. находиться в исправном состоянии, и на нем не выполняются никакие работы по обслуживанию, наладке или ремонту;
К2 – коэффициент использования технических возможностей, или коэффициент производительности оборудования. Он рассчитывается по формуле
Загруженность по скорости х Чистая загруженность;
К3 – коэффициент выхода годной продукции, или коэффициент качества.
Коэффициент общей эффективности оборудования (КОЭ) рассчитывается на основе фактических данных о работе оборудования и является наиболее точным и всесторонним по сравнению с другими применяемыми на производстве показателями – такими как загрузка оборудования, производительность и проч.
Следует заметить, что в производственной практике КОЭ, сохраняя свое название, часто переводится в процентное измерение. Например, КОЭ = 0,426, или 42,6%.
Пример 1 (рис. 1.2.2). Типичный результат работы Проектной команды ТРМ, полученный за 2-3 месяца в рамках текущих затрат и ресурсов (без привлечения инвестиций).
Вряд ли кто-то из руководителей откажется от «упавших с неба» 19% прироста эффективности оборудования, ведь это – увеличение выпуска продукции почти на 1/5, практически без затрат.
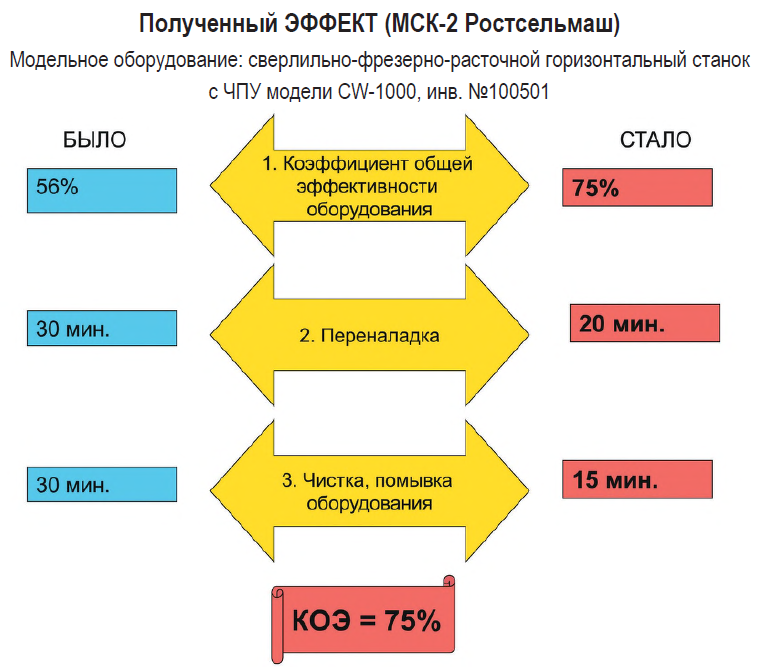
Пример 2 (рис. 1.2.3). Рост КОЭ производственной линии на 27% обеспечен также силами Проектной команды ТРМ за 3 месяца без капитальных затрат.
Если же принять во внимание, что это была единственная линия компании «Хенкель» в России, которая выпускала сухие чистящие средства (продуктовая линейка «Пемолюкс») и отсутствие «сереньких баночек с красной крышкой» на полках магазинов означало проигрыш рынка конкуренту – компании «Проктер энд Гэмбл» с его линейкой «Комет», то прирост эффективности на четверть был жизненно необходим и закрывал разницу между спросом и возможностями производства. В дальнейшем КОЭ этой линии был доведен до 90% и более, но уже силами не Проектной команды ТРМ, а Рабочей группы ТРМ (из рабочих), которая, работая на оборудовании, не только поддерживала достигнутые результаты, но и довела работу этой далеко не новой линии практически до идеального состояния.
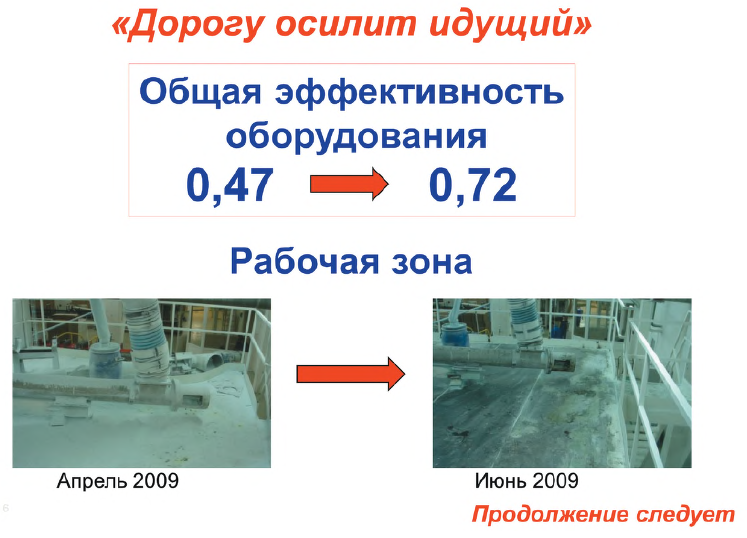
Пример 3 (рис. 1.2.4). Еще один результат: увеличение КОЭ до уровня, сопоставимого с японским. На украинской производственной фирме «Панда», производящей безалкогольную продукцию, за счет последовательного освоения трех первых шагов важнейшего направления системы ТРМ – «Самостоятельного обслуживания оборудования операторами (СООО)» прирост КОЭ составил 13%. Когда результат изначально уже выше 80%, – это достижение мирового класса.
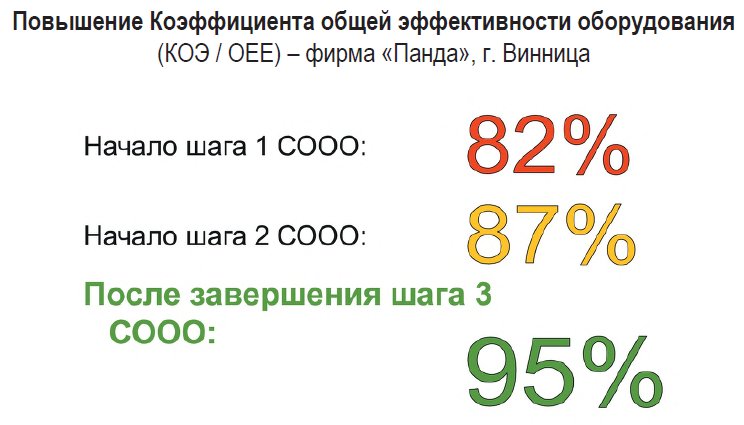
Что касается примера 3, приоткроем один из «секретов» достижения этих результатов. Источником повышения доступного времени работы линии и ее стабильной работы после переналадки в данном случае является сокращение времени чистки с одновременным повышением ее качества и безусловным соблюдением санитарно-гигиенических норм. Так как речь идет об изготовлении газированных напитков, малейшее нарушение микрофлоры на производственной линии может привести к катастрофическим последствиям как для продукта, в котором начнутся процессы брожения, так и для его потребителя и имиджа компании на этом высококонкурентном рынке (рис. 1.2.5).
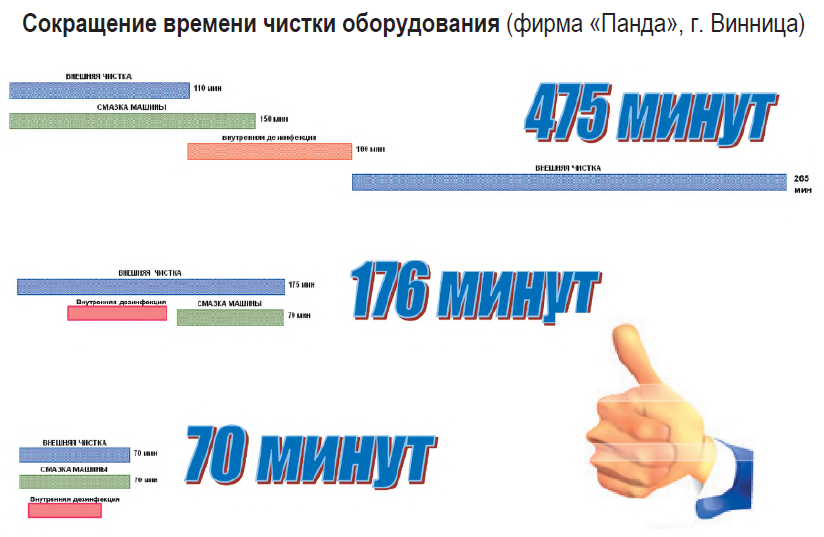
Пример 4 (рис. 1.2.6). В данном примере КОЭ/ОЕЕ рассчитан по методике компании «ИнБев» (как показатель GLY – общей урожайности линии) с учетом уровня загрузки линии. В пересчете на общепринятую методику он составит более 90%. При этом нормативное требование компании – 60% было перекрыто уже в первый год внедрения ТРМ. Такого показателя не было ни у одного из 12 предприятий России и Украины, входивших в один дивизион, их максимальные показатели находились на уровне 46-48%.
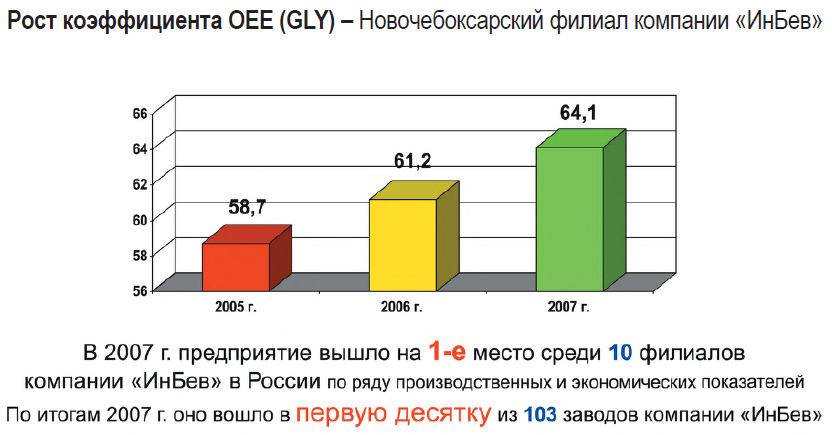
Пример 5 (рис. 1.2.7). Здесь мы видим комплексный результат повышения конкурентоспособности предприятия за счет полноформатного внедрения системы ТРМ, т.е. всех ее направлений. Система ТРМ была жизненно необходима московской фабрике «Большевик». Чтобы это заслуженное предприятие с далеко несовременным оборудованием, расположенное в центре Москвы, испытывающее сложности с логистикой, складскими помещениями, высокими экологическими требованиями, смогло не только сохраниться в телефонной книге, но еще и наращивать объемы производства и продаж, осваивать выпуск новых продуктов, укрепить свою конкурентоспособность.
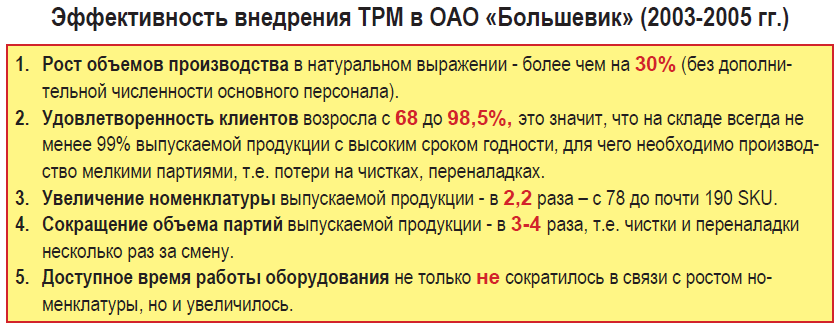
Пример 6 (рис. 1.2.8). Один из частных результатов внедрения ТРМ – реализация проекта «Быстрая переналадке (SMED)» на одном из производственных участков, где происходил рост номенклатуры и, соответственно, падала выработка. В проекте была проведена работа на 12 единицах оборудования, что позволило сократить время переналадки на участке на 70%.
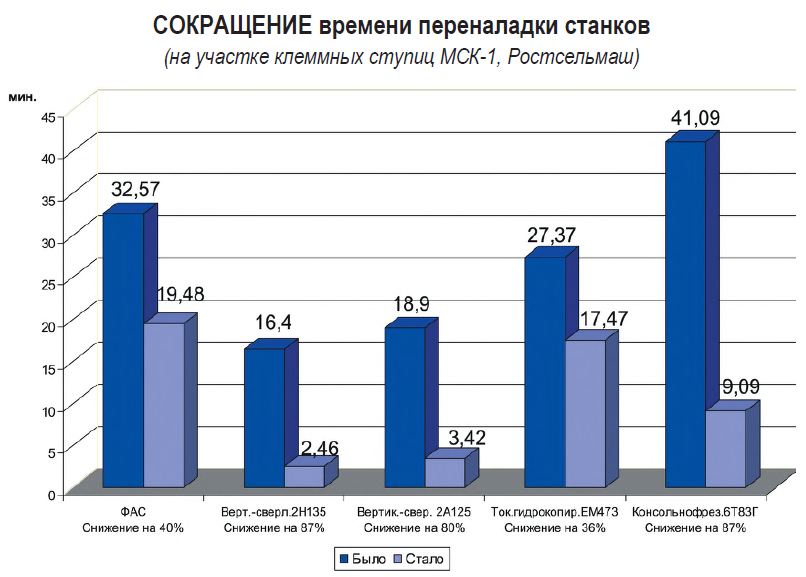
Пример 7 (рис. 1.2.9). И еще одни пример аналогичного проекта. При его реализации были задействованы не только технические, но и организационные решения, т.е. несколько направлений системы ТРМ. Сам проект длился почти 9 месяцев и был реализован на амбициозном производстве компании «Русский Стандарт Водка», где на линиях было собрано оборудование мирового уровня, но, как видно из графика, его переналадка занимала первоначально почти целую рабочую смену. По итогам проекта компании удалось сократить время переналадки в 3,3 раза.
Учитывая высокую рентабельность продукта и цену минуты простоя оборудования, после обсуждения первых результатов наблюдений за переналадкой руководство завода пошло на увеличение численности наладчиков, чтобы добиться сокращения потерь из-за взаимных ожиданий, т.е. несбалансированной работы трех исполнителей на переналадке линии, состоящей из 8 крупных агрегатов (не считая транспортеров и делителей потока).
Также на последнем этапе к процессу переналадки были подключены операторы, которые в обычном режиме в ней не участвовали. Это был первый такой опыт, поэтому он в данном примере связан еще и с обучением операторов выполнению правильных действий по переналадке. В дальнейшем, за рамками данного проекта, время переналадки удалось еще несколько сократить.
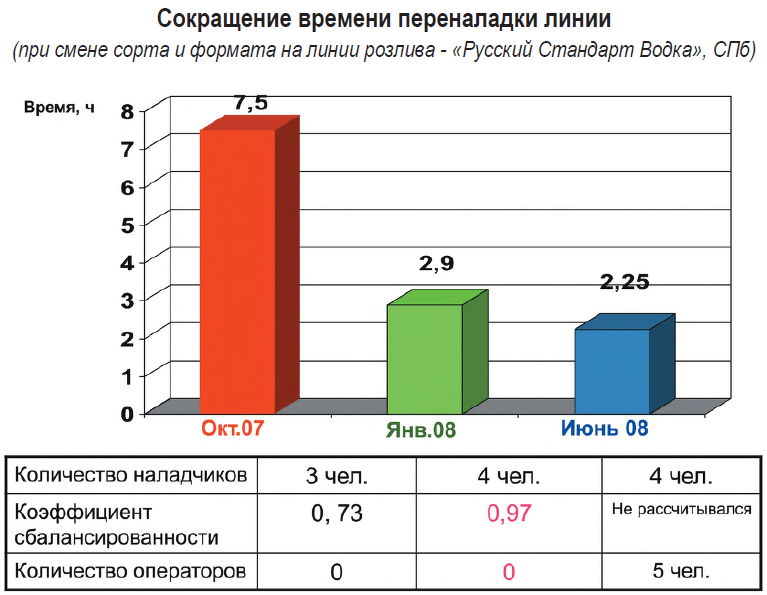
Пример 8 (рис. 1.2.10). Сокращение количества ремонтов (и поломок) подъемных агрегатов, выполняемых выездными ремонтными бригадами, в ООО «ТаграС-Рем-Сервис» в результате эффективного выполнения технического обслуживания (ТО) силами операторов, работающих на оборудовании.
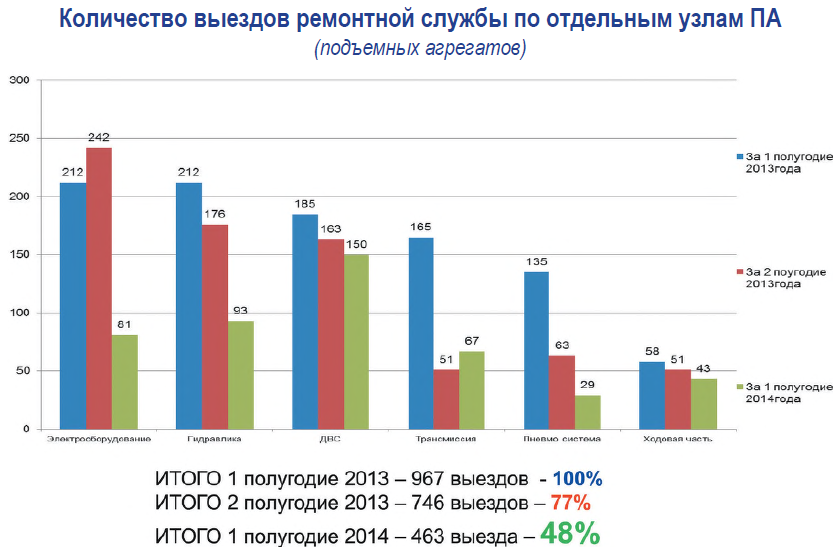
Пример 9 (рис. 1.2.11). Этот пример для тех, кто любит и умеет считать деньги, – насколько выгоднее выполнение ТО силами самих операторов по сравнению с привлечением сторонних исполнителей.
Но, ВНИМАНИЕ! Эту экономию, а не убытки от «убитого» оборудования вы получите только в том случае, если персонал, работающий на оборудовании, обучен выполнению ТО, заинтересован в правильном его выполнении, имеет для этого все необходимые ресурсы, а на самом оборудовании устранены все выявленные при первоначальной чистке неисправности.
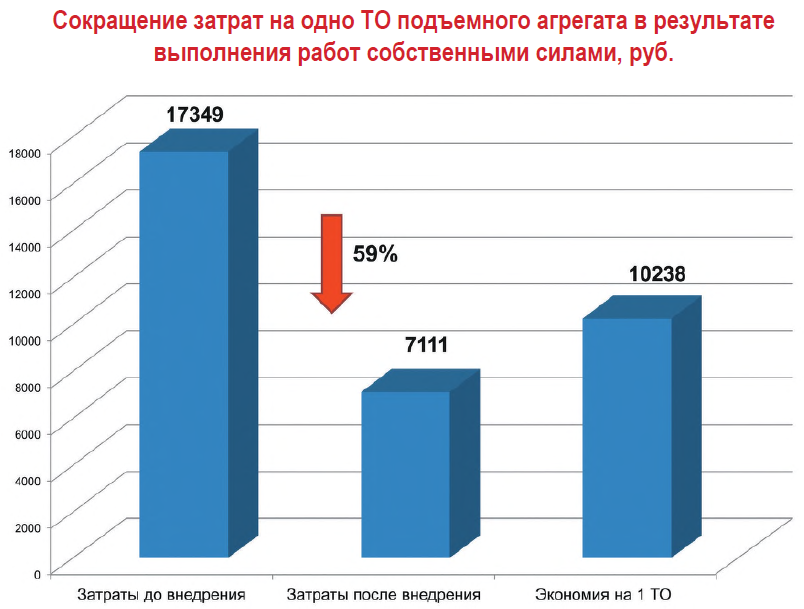
Ну что, уважаемый читатель, убедились, что и наши люди «не лыком шиты», а могут получить даже на оборудовании весьма почтенного срока службы результаты, которыми можно гордиться. Хочется попробовать и получить что-то подобное или лучше? Тогда – предлагаем двигаться дальше!