Многие энтузиасты бережливого производства знают эту аббревиатуру. Это название совместного предприятия Toyota и GM, завода во Фримонте, штат Калифорния.
Когда-то это было первое предприятие Toyota за пределами Японии, когда-то это предприятие было создано для того, чтобы General Motors научилась получать прибыль от производства небольших автомобилей. Потом его закрыли.
Недавно мне попалась замечательно рассказанная история NUMMI, вышедшая в радио-шоу «This American Life» на радиостанции WBEZ, Чикаго. Я потратил часа полтора, чтобы прочитать расшифровку записи передачи, но оно того определенно стоило. Если вам интересно, как Toyota переносила свою производственную систему в США и почему у General Motors не получилось ее растиражировать не смотря на то, что у GM был полный доступ ко всему, что происходило на этом заводе, то я предлагаю вам познакомиться с выдержками из этого радио-шоу.
Пятьдесят лет назад GM владел половиной американского авторынка. а сегодня — только 22% (чем-то напоминает наш ВАЗ). В 2015 году Consumer Reports отдала пальму первенства в надежности автомобильных марок маркам Lexus и Toyota. Первая из американских марок — Buick — на седьмом месте.
На заводе New United Motors Manufacturing Inc. (NUMMI) Toyota раскрыла перед GM все секреты — как именно производить самые лучшие, самые надежные автомобили. GM надеялся воспользоваться этими знаниями, чтобы распространить их по своим заводам по всей стране, по всему миру. Но этого не произошло, и в 2009 году GM стал банкротом, а 1 апреля 2010 года на заводе NUMMI была выпущена последняя машина, после чего завод был закрыт.
Действие первое
В момент создания NUMMI рыночная доля GM была в 7 раз больше, чем доля Toyota. Но у обоих компаний были проблемы, в решении которых им мог помочь конкурент. Для GM это было производство небольших автомобилей. Правительство США требовало снижать объем выхлопных газов, для того, чтобы соответствовать этим требованиям, GM должен был выпускать автомобили малых размеров (по американской классификации), но они всегда приносили только убытки и были паршивого качества. Toyota предложила партнерство, которое имело перед собой две цели. Первая — Toyota будет производить для GM малые автомобили, которые будут приносить прибыль. Вторая — Toyota хотела научить сотрудников GM тому, что называется Производственная Система Тойоты — TPS, открыть все секреты. К этому моменту Toyota была полностью японской компанией, располагающейся в местности, которая теперь называется Toyota City, а конгресс США, глядя на то, каких рыночных успехов стали достигать японские компании на американском рынке, стал ограничивать импорт автомобилей. Так что Toyota должна была научиться производить автомобили в США. Менеджеры Toyota очень тщательно подходили к решению этой задачи, они искали ответы на ключевые вопросы: как мы можем работать с американскими рабочими? как мы можем убедиться, что наша производственная система будет работать в США? И как эта система будет работать не в домашних условиях, где все поставщики «под боком», а когда основной объем деталей производится «за морем»?
В Японии рабочие и менеджмент работают над достижением целей компаний совместно, в США на предприятиях автопрома всегда велась война между менеджментмом и профсоюзом рабочих автопрома, UAW. На заводе во Фримонте это уже была не война, а рукопашный бой.
Завод во Фримонте был худшим заводом GM, и он был таким «по праву». На написание жалоб на менеджмент рабочие тратили больше времени, чем на производство автомобилей, там постоянно проходили забастовки, завод постоянно находился в состоянии хаоса. На заводе рабочий мог получить всё, что бы он ни пожелал: секс, наркотики, алкоголь, азартные игры — все было доступно. Рабочие были привязаны к этому заводу, т.к. рядом не было ни одного другого места работы, где они смогли бы получить такую работу, зарплату, соцпакет в соответствии с их образованием и навыками. Они были там как в ловушке. Так что это была работа на всю жизнь, а профсоюз был их защитником. Поэтому возможность получить что-то незаконное рассматривалось просто как развлечение. Профсоюз был непробиваемой защитой для рабочих — нельзя было уволить никого, кто находился под его защитой. Прогулы были нормой. В некоторые дни менеджеры не могли набрать столько рабочих, чтобы можно было запустить конвейер. Тогда они шли на улицу и вытаскивали из бара напротив завода нескольких завсегдатаев, чтобы поставить их на рабочие места.
Рабочие писали жалобы по любому поводу: если не твой прямой начальник просит тебя что-то помыть, или если он влез в не свое дело, неважно что это было. Рабочие делали такое, что кажется немыслимым на нормальном предприятии: сборщик мог оставить банку из под колы в дверной панели, чтобы она бренчала и раздражала покупателя, они царапали машины, один рабочий оставил незатянутыми болты в подвеске более 400 автомобилей, потому что его отстранили от работы, когда он был пьян.
В 1982 году GM закрыла завод. На следующий год, когда GM и Toyota планировали открыть завод снова, они сделали нечто неожиданное — они наняли тех же самых профсоюзных лидеров, которые вели борьбу с менеджментом GM. Профсоюзный лидер Брюс Ли (не всемирно известный спортсмен и актер, а другой, полный тезка) на встрече с Ейджи Тойодой (тогда он был президентом компании) потребовал, чтобы в качестве первых 50 человек приняли профсоюзных лидеров. Он считал, что проблема не в людях, а в системе. Японцы согласились. Ли пошел к своим людям и сказал, что завод будет другим, новый менеджмент, новые правила, которые установят японцы. Люди хотели, чтобы всё осталось как прежде. Но у нового руководства был козырь — все эти люди отчаянно нуждались в работе. Когда NUMMI открылся в 1984 году, 85% сотрудников были бывшими сотрудниками завода GM. Но Toyota отлично подготовилась к этому моменту. Всё это время Toyota возила рабочих группами по 30 человек в Японию и учила их производить автомобили по-японски.
Когда первая группа американских рабочих приехала в Японию, никто не знал, что произойдет и чем это закончится. Это было событие, и для японцев, и для американцев. Многие из рабочих никогда до этого вообще не летали, никто до этого не бывал в Японии. Одно из первых наблюдений, которые сделали японцы, заключалось в том, что американцы по своим габаритам значительно превосходят японцев, и тратят на сборочном конвейере на 1-2 секунды больше, потому что им требуется больше времени просто для того, чтобы влезть в машину и вылезть из нее.
Ключевой принцип, которому Тойота пыталась научить рабочих, это то, что звучит как пустой слоган — командная работа. В GM супервайзеры руководили большими группами рабочих, на заводе в Такаока команды состоят из 4-5 человек, которые регулярно меняются на своих рабочих местах, а лидер команды включается в работу при первом же признаке проблем.
Рабочие проводили в Японии две недели и работали на сборочной линии. Рабочие очень старались показать свои навыки, поскольку они работали на сборке в США, им было сложно вписаться в заданный ритм, и рано или поздно за их спиной появлялся лидер команды и спрашивал: «хотите, я вам помогу?» Это было новым, т.к. в США никто им не предлагал помощь, и они кричали на лидера, чтобы они им не мешал.
Японцы хотели показать им то, как у них принято работать. Когда у американских рабочих появлялись проблемы, их спрашивали: могут ли они предложить что-то, чтобы улучшить ситуацию и сделать так, чтобы проблемы не повторялись. Американцы стали делать предложения — другой, более удобный для работы инструмент, другое место для хранения болтов, место для сидения, чтобы было удобнее достать какой-то узел. Американские рабочие не верили в то, что происходило после этого — никто из них не мог вспомнить, чтобы у него просили совета, японцы реально хотели знать, что думает американец, японцы слушали, затем исчезали и возвращались с готовым решением — инструментом, который описал рабочий, или приспособлением. И они говорили: «попробуй».
Работа стандартизировалась. Все действия рабочих многократно оттачивалась, чтобы уменьшить количество движений, расстояния, усилия и так далее.
На заводе GM существовало одно правило, которое никто не имел права нарушить — конвейер не должен останавливаться никогда. Ни в коем случае: если кого-то хватил инфаркт, отпихни его с дороги и продолжай работать. Ни в коем случае нельзя останавливаться.
Этому было «разумное» обоснование. Менеджмент считал, что рабочие не хотят работать, что они хотят сидеть и играть в карты. Если конвейер остановится — это будет бесплатный перерыв для рабочих. Поэтому конвейер не должен останавливаться. Это началось с Генри Форда, который считал, что главное — выпустить объем продукции, выкатить машину за ворота цеха, а дальше уже можно исправить все недоделки.
За годы это привело к тому, что люди вообще перестали обращать внимание на то, что движется по конвейеру. Говорили о том, что на заводе во Фримонте с конвейера могла сойти машина одной модели с капотом от другой машины, у машины могло не быть руля или тормозов…
Философия Тойоты была полной противоположностью — качество, а не количество. У каждого рабочего под рукой есть способ остановить весь конвейер — шнур андон. Когда кто-то дергает его, звучит мелодичный сигнал и на табло загорается лампочка, обозначающая конкретное рабочее место. Лидер команды должен помочь рабочему устранить проблему. Если он не сможет это сделать за определенное время, конвейер останавливается. И эти мелодичные сигналы звучат на японских заводах постоянно. Задача всей системы — устранить проблему сразу в тот момент, когда она возникла.
Один из американских рабочих рассказал, какие чувства он испытал, когда первый раз дернул шнур андон. Он сильно нервничал, ведь он много лет работал на конвейере в условиях, что конвейер не должен останавливаться. Ему попалась сорванная резьба для винта, так на его глазах лидер команды исправил проблему, предотвратив кучу работы по перемещению автомобиля на ремонтную площадку, по выяснению того, в чем, собственно, заключалась проблема, и придумыванию, как ее устранить вне условий конвейера.
Перед отъездом обратно американцы и японцы устроили «корпоратив» с суши, и расставались буквально со слезами на глазах. Как сказал один из американских рабочих японцам «благодаря вам мы теперь уверены в нашем успехе».
Для американцев принцип остановки конвейера означал другие отношения между менеджерами и рабочими. Он устанавливал правила командной работы. Когда в декабре 1984 года первый автомобиль Chevy Nova сошел с конвейера, один из лидеров профсоюза сказал: «мы на пороге новых отношений между менеджментом и рабочими. Слишком долго американских рабочих унижали, критиковали, обзывали за то, что они производят плохую продукцию.»
Брюс Ли высказался об этом событии так: «О, я так горжусь ими, вы даже не можете поверить. Меня удивляет не тот факт, что они сделали это, а то, как быстро они это сделали. Это было потрясающе. Это были те же самые люди, что и прежде — я имею в виду, черт возьми, что они, в частности, отказались от своего жизненного кредо делать работу менеджеров GM невыносимой. И знаете, они были старыми, они были жирными. Потому что мы не посылали туда молодых сотрудников.»
Им не нужно было ждать год, два года, чтобы начать делать качественную продукцию. Они добились высокого качества с самого начала. Через 3 месяца автомобили, сходящие с конвейера, достигли практически идеального качества. Для GM было важно снижение затрат. И одно из исследований показало, что в старой системе для производства той же модели нужно на 50% больше рабочих.
Жалобы и прогулы прекратились. Рабочие предпочли командную работу старой культуре непрерывной борьбы, которая была на прежнем заводе. Некоторые говорили, что они впервые получают удовольствие от работы. Рабочие с завода оставляли почтовые открытки под дворниками автомобилей Chevy Nova, которые они встречали в городе или где-то в поездках с просьбой к владельцу поделиться своими впечатлениями от машины. Некоторые специально ездили к дилеру Шевроле, чтобы посмотреть на выставленные на продажу автомобили, в сборке которых они участвовали, чтобы посидеть в них немного.
NUMMI смогла реализовать обе цели, которые ставила Toyota: японцы научили американских рабочих собирать малые автомобили высокого качества и укоренили свою производственную систему в американской культуре.
Действие второе
GM получила первый результат от совместного предприятия NUMMI — они начали делать высококачественные малые автомобили. Второй задачей было распространение этого опыта на другие заводы. Менеджмент GM направил на завод NUMMI с самого начала 16 восходящих звезд, которых потом назвали «Коммандос NUMMI», от них ожидали, что вернувшись на свои предприятия они изменят компанию. Если GM сможет встроить эту производственную систему во множество своих предприятий, каждое из маленьких изменений добавит к результатам GM миллиарды долларов. Но когда коммандос вернулись к своей работы, ничего не произошло. Никто не спросил их «в чем заключается секрет?», «как можно это использовать для повышения наших результатов?», никто ни о чем не спросил.
Не было никакого плана, как применить полученные знания. В итоге некоторые из коммандос просто уволились.
Первая попытка что-то предпринять возникла на заводе в Ван Найс. Заводу грозило закрытие, и его менеджер, побывав на NUMMI, решил, что японская система может спасти предприятие. Но у него не было всех преимуществ Фримонта. Toyota не участвовала в этом проекте, GM должен был провести преобразования самостоятельно.
Менеджер считал, что отсутствие альтернативы заставит его сотрудников двигаться, изменяться. На заводе Ван Найс производили Firebirds и Camaro, и репутация завода была немногим лучше, чем у Фримонта: низкое качество автомобилей, борьба с профсоюзом, саботаж. Менеджер завода в Ван Найс, Эрни Шэфер, пригласил профсоюзного лидера завода NUMMI, Брюса Ли, помочь ему в преобразованиях.
Они остановили завод на две недели для того, чтобы провести обучение тому, что такое командная работа и управление качеством. Рабочие, которые не ездили в Японию, не прощались в слезах со своими японскими коллегами, которые не видели, как эффективно всё это работает, отнеслись к изменениям крайне скептически.
Рабочие не верили, что завод закроют. У них не было ощущения неизбежности изменений. Это было одно из важнейших отличий. Завод в Ван Найс не закрывали. Гораздо проще было убедить рабочих в необходимости изменений, если бы их лишили их работы, а затем предложили бы вернуться. Без этого многие видели в тойотовской системе угрозу.
И в этом был смысл. Ожидалось, что с помощью японской системы численность персонала в Ван Найс сократят на четверть, потому что завод станет более эффективным и нужно будет меньше рабочих рук. Кроме того, взаимозаменяемость в командах нарушала права старшинства, на которых стоял профсоюз. Люди годами работали на заводе, чтобы получить свое право старшинства, которое давало им дополнительные привилегии, а в новой системе менеджер мог уволить любого. Профсоюз утрачивал свое значение. Чтобы сохранить команду, каждый ее член должен был удостовериться, что команда крепка, и появлялось желание устранять слабые звенья. Люди переставали держаться друг за друга, забывали, для чего они, собственно, объединялись в профсоюз.
Но в Ван Найсе не только члены профсоюза сопротивлялись внедрению японской системы. Точно так же сопротивлялся и менеджмент. Менеджеры стремились защитить свои привилегии. Они сопротивлялись введению правила остановки конвейера в случае возникновения проблем, т.к. их премии зависели от того, сколько автомобилей выпускает завод, независимо от того, какого качества эти автомобили. Проблемой было даже то, что рабочие и менеджеры в новых условиях должны были пользоваться одними и теми же столовыми и парковками. Менеджеры среднего звена угрожали увольнением только потому, что им нужно пройти лишних двадцать метров по парковке.
Введению новой системы сопротивлялись все сотрудники завода. Но кроме этого, Эрни Шэфер столкнулся еще с одной проблемой, которой не было на заводе NUMMI. Рабочие не могли добиться лучшего качества сборки автомобилей из тех деталей, которые они получали. Детали автомобилей NUMMI поступали из Японии, и там не было проблем с качеством. В Ван Найсе всё было по другому. Инициаторы изменений осознали, что они не могут изменить один завод, не изменив всю систему.
В командной работе важны непрерывные улучшения. Если команда обнаруживает, что используемые детали непригодны для использования, она сообщает своему руководителю, тот ставит в известность поставщика, который исправляет проблему. Но поставщики завода Ван Найс никогда так не работали. Если Эрни Шэфер просил поставщика что-то изменить, тому было наплевать. Если Эрни звонил в Детройт Большому Боссу, тот только удивлялся: «другие заводы это устраивает, а тебя не устраивает, ты что — особенный?»
В GM все подразделения очень сильно обособлены. Там просто принято «перекидывать работу через стену». Если ты проектируешь автомобиль, ты делаешь дизайн и перебрасываешь его через стену в отдел подготовки производства. И если что-то не работает, или что-то невозможно собрать, это их проблема, а не твоя.
И люди, которые пытались что-то изменить, оказались в ситуации, когда даже их лидер, менеджер завода, был вынужден признать: «Смотрите, предполагается, что это работает таким образом. И это моя проблема. Я не могу ее решить, поэтому нам придется с этим жить».
Шэфер понял, что хотя Toyota дала всем сотрудникам GM возможность приходить на завод NUMMI и изучать, как всё работает, никто не понял того, что весь завод работает только благодаря мощной системе, которая обеспечивала функционирование завода.
Другие попытки перенести опыт NUMMI на другие предприятия тоже не вели к успеху. Один из ИТ-директоров, побывав на NUMMI, написал отчет, который можно было бы назвать «Здесь это не работает». Если бы он согласился применить новую систему, ему пришлось бы уволить половину своих сотрудников, поскольку они бы уже не были нужны. А это утрата власти, которая очень ценится в GM. Оказалось, что в GM нет ни одного человека, который был бы способен провести радикальные преобразования в этих мини-империях, которые сформировались за десятилетия существования GM.
Многие бывшие сотрудники NUMMI ощущали разочарование из-за того, что видели отсутствие срочности в действия GM. Менеджеры GM отказывались признавать угрозу со стороны конкурентов даже не смотря на то, что доля рынка GM сократилась с 47% в 1970-ых до 35% всего за десять лет. Все три американские корпорации, GM, Ford и Crysler считали, что клиенты убеждены в плохом качестве их машин не потому, что машины на самом деле плохи, а потому что на покупателей негативно воздействуют СМИ. GM увлекся другими масштабными проектами — купил EDS, потом 5 млрд. долларов ушло на покупку Hugehs Aircraft, затем было объявлено, что будущее — за работами. GM запустила новую марку автомобилей — Saturn, которую разрекламировали гораздо лучше, чем производили (сейчас её уже не существует). И потом наступил провал продаж.
В 1992 году GM потерял 23,5 млрд. долларов — крупнейший убыток за всю историю США. Действия совета директоров назвали «кровавой баней в совете директоров» — было уволено большое количество руководителей. Это был повод серьезно переосмыслить корпоративную политику, стратегию.
На должность CEO был назначен Джек Смит. Он начал быстрое внедрение TPS. Быстрое — по стандартам GM, но оно было совсем небыстрое. Много лет спустя он сказал, что желал бы, чтобы все происходило намного быстрее. Это было все равно, что развернуть линкор. И даже при том, что CEO GM дал прямое указание начать преобразование, разница между NUMMI и остальным GM была так велика, что люди просто не понимали, с чего начать.
Один вице-президент дал команду обмерить каждый дюйм завода NUMMI и сделать все остальные заводы похожими на него. «Не может быть никаких извинений, что мы другие, нежели NUMMI, что наше качество хуже или наша производительность ниже, потому что вы скопируете всё, что увидите».
Есть вещи, которые нельзя скопировать, даже сфотографировать: мотивацию сотрудников, хорошие отношения между менеджерами и профсоюзом, и т.д.
Первым делом везде вводили шнур андон. Но он не менял культуру. Рабочие и менеджеры продолжали противостояние. Если кто-то из рабочих дергал за шнур — на него орали. На некоторых заводах этот шнур просто обрезали.
Вторая попытка заключалась во введении принципа командной работы. Компания тратила усилия, чтобы обучить принципам командной работы, но директора заводов все равно могли управлять ими на свое усмотрение.
Многие по-прежнему не видели необходимости в изменениях. Позднее, в 1990-ых, компания получила большую прибыль от продаж пикапов и внедорожников, и поэтому потеря рыночной доли стала не столь важна. Более глубоких изменений удавалось добиться тем, кто уезжал из США — в Германии и Бразилии удалось достичь гораздо более значительных изменений. Бразильское отделение GM стало одним из наиболее прибыльных в 1994-1997 годах. В США же потребовалось 15 лет, чтобы изменения только начались.
Изменения начали проявляться благодаря тому, что на NUMMI побывали уже очень многие, и это масштабное ознакомление с иной производственной культурой наконец-то начало давать плоды, как снежный ком, всё больше и больше людей стали понимать, как им нужно действовать.
В начале 2000-ых GM разработала свою производственную модель, которую назвала Global manufacturing system, основанную на японских принципах, и начала распространять ее по всем заводам. Качество автомобилей стало улучшаться, хотя в целом оно всё еще было очень низким. Хуже того, хотя GM и становилась лучше, ее конкуренты по прежнему уходили всё дальше и дальше вперед.
В итоге, наступила рецессия 2008 года. Через год GM был объявлен банкротом. Это стоило налогоплательщикам 50 млрд. долларов. Ирония заключается в том, что перед банкротством GM был, возможно, в самом лучшем состоянии, чем когда бы то ни было.
Если бы GM смог применить опыт NUMMI, он мог бы выпускать более качественные и надежные автомобили, и это помогло бы сохранить большую рыночную долю. Но надежность и качество были не единственными проблемами GM. Контракт на медобслуживание между GM и профсоюзом UAW был таким, что в 2007 году на его покрытие с продажи каждого автомобиля, произведенного в США, уходило 1600 долларов. И, наконец, GM прозевал появление гибридных автомобилей. Компания сконцентировалась на больших машинах — внедрожниках и пикапах, продажи которых рухнули, когда галлон бензина стал стоить 4 доллара.
Еще один поворот истории заключается в том, что за последние 10 лет, когда GM пытался стать больше похожим на Toyota, сама Toyota стала больше похожей на GM. В 2008 году Toyota стала самым крупным в мире производителем автомобилей. Toyota погналась за количеством вместо качества. И нынешний CEO Toyota, Акио Тойода, правнук основателя компании, выступая на слушаниях в Конгрессе США в 2010 году по поводу проблемы внезапного ускорения автомобилей, заявил, что ошибкой компании было то, что она слишком быстро росла.
GM потребовалось 15 лет, чтобы начать относиться серьезно к опыту NUMMI, и еще 10 лет компания медленно внедряет то, чему научилась. Всё это время NUMMI продолжал делать автомобили — в среднем 6000 в неделю, в две смены. Toyota получила то, что хотела. Через год после запуска NUMMI, Toyota начала открывать заводы в США, пользуясь теми знаниями, которые получила при запуске NUMMI.
GM и Toyota продолжали совместно управлять заводом до 2009 года, до банкротства GM. В 2010 году Toyota решила закрыть завод. Это был единственный завод Toyota в США, на котором был профсоюз. Это был первый завод, который Toyota закрыла за 73 года своей истории.
Теперь NUMMI — это наследие. И это не только символ того, что на GM много шло не так, как надо. Это еще и реально отличный завод, который выпустил почти 8 млн автомобилей.
Жизнь после NUMMI
20 мая 2010 года Toyota и Tesla анонсировали партнерство с целью разработки автомобилей с электрическим приводом, в рамках которого Tesla частично выкупала площадку NUMMI. Завод официально перешел под управление Tesla 19 октября 2010 года, 27 октября 2010 года завод был открыт. Первая собранная на новом заводе машина Tesla Model S была передана клиенту 22 июня 2012 года.
Фото завода NUMMI взято отсюда, диаграмма надежности автомобильных марок — отсюда, фото завода Tesla — отсюда.
Оригинал стенограммы радиошоу на английском языке можно найти здесь. Послушать запись 403 эпизода шоу «This Americn Life» в оригинале можно здесь.
Кому это может быть интересно
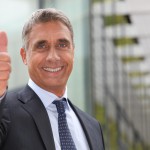
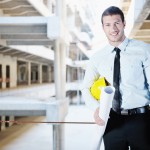
Узнать, кто эти люди…
Валерий, спасибо за интересный материал! Уверен, что для Российской аудитории весьма полезно подумать над этим опытом.
В подавляющем большинстве проекты такого класса в России могут даже инициироваться первым лицом, но на этом приверженность заканчивается и не происходит изменений ментальных моделей первого лица, что и является главной причиной неудач.
Изменение взаимоотношений между менеджментом и рабочими — первое условие. Второе — системный подход, т. е. понимание, что сумма локальных оптимумов не даёт оптимума системы.
В исходнике был и такой момент, который подтверждает ваш комментарий:
Руководители GM с самого начала скептически относились к совместному проекту. Кажется это описал Джеффри Лайкер, примерно такими словами: «Они думали так: может быть что-то будет полезным, может быть — нет, но вредно не будет в любом случае». Другими словами, это означает: «ну ладно, пусть будет, а там посмотрим». Конечно же в такой логике места для изменения собственного мышления в рассуждениях менеджера не остаётся…
Красочный триллер. Неясно одно теперь у Тесла какое качество по сравнению с NUMMY и где производятся их компоненты?
Андрей, по поводу качества можете посмотреть ежегодные отчеты Consumer Reports. Информацию о происхождении деталей вряд ли удастся найти так легко, хотя где Tesla делает батареи, мне кажется, узнать можно.
Я думаю, многие читатели будут вам благодарны, если вы напишете в комментариях то, что сможете узнать про качество автомобилей Tesla.
Валерий, Спасибо большое! Супер интересная информацию.
Илья, я думаю, это один из лучших кейсов, которые я видел за несколько последних лет…
Материал очень понравился. Труд титанический. Очень большое спасибо!
Не мог пройти мимо этого материала при всей нехватки времени. Так что не за что. 😉
Валера, спасибо огромное за материал!
Безумно интересно было прочитать, что же случилось с тем самым заводом Toyota-GM.
Я думаю, что эту картину можно переложить и на современные реалии, когда многие хотят «как на Тойоте». И историю всего GM могут повторить многие: просто вопрос масштаба — небольшие компании или корпорации. Результат один.
Это то, что лишено метки «менталитета». Принципы управления — одни, люди — разные.
Еще меня поразила связь GM — Nummi — Tesla. Ведь по факту, те же работники, которые работали на Nummi с большой вероятностью и начали работать на Tesla.
Вероятная преемственность радует)
Да, очень интересный материал. Давно такого не попадалось…
Отличный материал, продолжение Джеффри Лайкера 🙂