Сергей Турусов, работавший ранее директором по развитию производственных систем БрАЗа (читайте книгу «Сломай стереотип! Производственная система Братского Алюминиевого Завода»), ОМК, а теперь зам. управляющего директора по развитию производственной системы концерна Калашников, запостил 27 апреля в Facebook статью про четыре вида потерь. В ней много интересного, поэтому я решил её подробно разобрать.
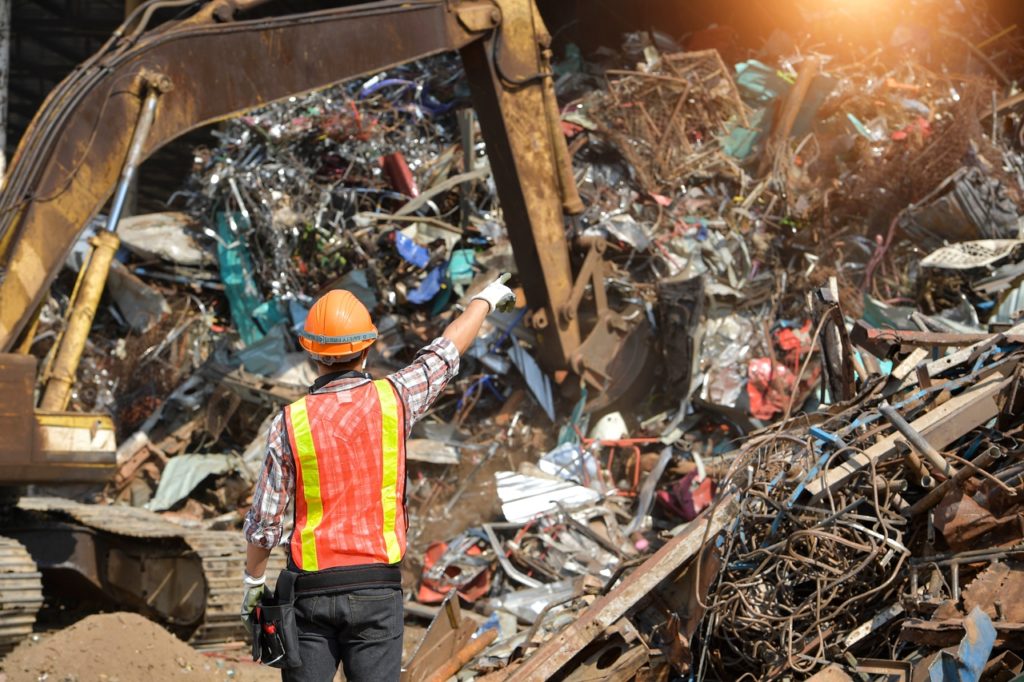
Провокационное заявление
Статья начинается сразу с провокационного заявления. Ну, а зачем тянуть-то.
«Существует четыре вида потерь, которые определяют эффективность работы любого бизнеса. Не семь, как у японцев, а именно четыре. Это если рассматривать потери с позиции эффективного функционирования потока создания ценности для клиента, то бишь бизнеса.»
Очень двусмысленное окончание предложения, так и читается: для клиента, то бишь бизнеса. Кто клиент потока создания ценности? Бизнес? Определённо, такая точка зрения есть. И она определённо не «бережливая».
Но, скорее всего, Сергей хотел написать так: «Это если рассматривать потери с позиции эффективного функционирования потока создания ценности для клиента, то бишь с позиции бизнеса». Лишние повторения слов имеют значение, не так ли?
Суть провокации
Ну а что «по сути»? Семь японских видов потерь — они тоже с позиции эффективного функционирования создания ценности для клиента сформулированы. И если Сергей «секвестирует» их до четырёх, значит что-то ушло «в величины второго порядка», как говорят математики. Это когда влияние есть, но оно какое-то незначительное, и, по сути, им можно пренебречь. Для упрощения расчётов.
Сергей выделяет среди прочих факторов, влияющих на эффективность потока, его синхронность:
«Чем выше синхронность (согласованность) функционирования рабочих мест, тем выше эффективность потока создания ценности.»
Далее идёт объяснение того, почему синхронность функционирования рабочих мест страдает и почему, собственно, возникают проблемы:
«Но каждое рабочее место имеет свои вариации (изменчивость), которые… тем самым приводят к его разбалансировке/рассогласованию/ресинхронизации. Разбалансировка может достигнуть таких значений, что поток создания ценности может вообще остановится… Поэтому, для того чтобы поток создания ценности не остановился в условиях внешних и внутренних вариаций, бизнес создает избыточные запасы на их компенсацию – в сырье и материалах, в персонале, в оборудовании и технике, в сроках исполнения заказав. Это и есть те самые «четыре вида потерь», которые снижают производительность бизнеса и увеличивают стоимость потока создания ценности.»
Ага. Проблемы потока — это его разбалансировка. Она возникает из-за вариаций. Чтобы их компенсировать нужны избыточные запасы четырех видов, которые, собственно, и являются потерями (по Сергею Турусову).
Четыре или семь
Аргументация «почему четыре, а не семь» строится на остылке к «знающим людям» и «прагматичности»:
«Японцы говорят про «семь видов потерь», а прагматичные европейцы – про «четыре вида потерь». Много не значит, лучше. Мы не можем устранять все потери, нет столько ресурсов. Целесообразно сконцентрироваться на устранении тех потерь, которые в первую очередь снижают ценность для клиента, то бишь на «четырех видах потерь».»
Ну, раз европейцы сказали, значит так и есть.
Нельзя устранить все потери, это факт. Поэтому можно проигнорировать то, что не критично для бизнеса.
Давайте сравним два списка.
Вот потери «от Тайити Оно»:
- Дефекты
- Запасы
- Движения людей
- Перемещения материалов
- Ожидания
- Избыточная обработка
- Перепроизводство
Вот потери «от Сергея Турусова и европейцев». Избыточные запасы:
- сырья и материалов
- персонала
- оборудования и техники
- времени исполнения заказов
Попробуем разобраться, какие из семи японских потерь покрываются четырьмя европейскими. Это поможет понять, а не упускают ли что-то европейцы.
Избыточные запасы в сырье и материалах
Это, на самом деле, точный аналог японских потерь типа «запасы».
«…могли бы эти «замороженные» деньги куда-нибудь вложить и получить дополнительный доход. Но это происходит только в том случае, если инфляции издержек (а стоимость сырья и материалов как правило растет со временем) будет ниже, чем полученный доход. А если наоборот, инфляция издержек будет больше… мы можем получить отрицательный эффект, но уже при минимальных запасах. Получается, что запасы в сырье и материалах в определенные периоды времени с финансовой точки зрения выгодно держать на высоком уровне. Здесь есть над чем подумать.»
Замечание насчет высокой инфляции издержек стоит учитывать в наше время, ведь многие предприятия как раз столкнулись с тем, что сырье и материалы стали стоить ощутимо дороже (а в некоторых случаях «их вообще невозможно купить ни за какие деньги»).
Однако я сюда добавил бы еще один важный аспект. Запасы (и их уровень) очень важны в стабильном состоянии ассортимента. Если ассортимент продуктов и услуг не меняется достаточно долго, вам нужно обеспечивать стабильное наличие сырья и материалов для их производства. И тогда в некоторых случаях нужно иметь большой запас, чтобы потом не кусать локти.
Но вот вам вопрос: какие отрасли работают постоянно с одним и тем же сырьем, одними и теми же материалами в течение долгих периодов времени? Это точно не все отрасли, и некоторые из известных мне отраслей настолько динамичны, что ассортимент в них меняется по нескольку раз в год. В условиях вариативности внешнего рынка выражения «остаться с запасами» и «остаться с носом» могут иметь вполне одинаковое значение.
Избыточные запасы в персонале
«…если усредненная вариативность потока составляет 30%, мы вынуждены держать примерно на эту же величину избыток персонала. А если доля затрат на персонал в себестоимости составляет 50%, то избыточный персонал приводит к увеличению стоимости потока на 15%.»
Если честно, я давно не видел предприятий, которые не испытывают нехватку в персонале и жалуются на то, что вынуждены держать лишних людей. Демографическая ситуация на рынке трудовых ресурсов слишком сложная, чтобы можно было себе это позволить.
Но какие «японские потери» соотносятся с этим видом «европейских потерь»?
Если вдруг, вопреки ожиданиям, у вас образовалось несколько лишних людей, то они начинают генерировать большой комплекс «японских потерь» просто, чтобы заняться хотя бы чем-то.
Первое, это, конечно, ожидания. Ожидания человека, который ничего не делает.
Если такой человек решает вдруг, что надо имитировать деятельность, чтобы тебя не уволили, и даже не подумали о том, чтобы тебя уволить, то дальше появляются «движения людей» (ходит туда-сюда), «перемещения материалов» (носит туда-сюда), «избыточная обработка» (красит снег или протирает пыль после каждого «чиха»), «перепроизводство» (делает больше, чтобы заполнить время). При этом — это не полное соответствие, т.е. не все «движения людей» появляются из-за лишних людей, как и «избыточная обработка» не всегда возникает из-за лишнего свободного времени у исполнителя.
Поэтому потери-«избыточные люди» не покрывают полностью перечисленные 5 японских видов потерь.
Избыточные запасы в оборудовании и технике
Если кто-то не в курсе, то бережливое производство в качестве буфера для вариативности в первую очередь использует мощности оборудования. Поэтому OEE никогда не должен быть близок к 100%. И полная загрузка станков — это проблема, которую (с точки зрения бережливого производства) надо решать, высвобождая мощности.
Тем не менее, избыточные ресурсы оборудования могут приводить к появлению «японских потерь»: «ожидания» оборудования и «избыточная обработка» (если наладчик решил воспользоваться «лишней мощностью», чтобы качественней обработать сырьё/материалы).
Если избыточным оборудованием является транспортная техника (погрузчики, краны) и одновременно есть избыточный персонал, то оборудование может так же участвовать в потерях типа «движения людей» и «перемещения материалов».
Интересно, что Сергей в связи с потерями в форме избыточных ресурсов оборудования и техники пишет, в основном, не про потери, которые возникают в потоке, а про финансовые расходы:
«Здесь и разовые потери на приобретение оборудования и техники для компенсации вариаций, и постоянные — на его обслуживание».
Избыточные запасы по времени исполнения заказов
«… мы можем выпустить партию продукции в мае месяце, но из-за внешних и внутренних вариаций вынуждены увеличивать нормативный производственных цикл на непредвиденные ситуации… Это вид потерь напрямую влияет не только на издержки, но и на объемы производства, то бишь на выручку бизнеса.»
Основной аналог в «японских потерях» — это ожидания. О чем говорит Сергей, так это о ситуациях, когда производство невозможно продолжать, потому что для этого чего-то не хватает (из-за вариативности процессов). Т.е. это антипод «европейских потерь-запасов», которые вроде как были лишними.
Что касается других видов японских потерь, то они скорее могут быть причинами избыточных запасов по времени выполнения заказов, из-за которых предприятие целенаправленно «удлиняет» сроки производства.
Для какого производства подходит такой набор потерь?
Если вы задумаетесь над описываемыми ситуациями, то оказывается, что речь идёт о бизнесе, который страдает из-за избытка запасов, в котором могут периодически (из-за вариативности спроса) возникать излишки персонала и техники, и которое берёт приличные запасы времени на исполнение заказов.
Что это за производства? Вот такие: большое, не новое, работающее на давно существующем рынке, как минимум частично монополизировавшие свою часть рынка (сегмент рынка).
Почему я так думаю? Небольшие и средние предприятия не могут себе позволить даже шансов лишнего персонала. Новые предприятия не создают запасов оборудования. Предприятия, которые работают на недавно возникших рынках тоже обычно не имеют избытка оборудования и персонала. А если нет возможности диктовать клиентам сроки, то невозможно и удлинять сроки выполнения заказов «на всякий случай».
Собственно, в опыте Сергея именно такие (или близкие к этому) «крупняки»: Братский Алюминиевый Завод, Объединенная Металлургическая Компания, концерн Калашников.
Какие рекомендации даёт автор
«необходимо повышать уровень стандартизированной работы для снижения вариаций на рабочих местах»
и
«повышать скорость реакции бизнеса на внешние и внутренние вариации»
В общем, тут всё логично. Если у нас есть лишние ресурсы на покрытие вариаций, то за счет стандартизации можно снизить внутренние вариации. А поскольку есть те вариации, на которые стандартизацией не повлиять, то надо просто быстрее реагировать на изменения, а не ныть на тему «вот в прошлом веке трава была зеленее, клиент добрее, а комиссионные побогаче».
Продолжение рекомендаций с легким налётом авантюризма
«Раз мы не можем устранить вариации, нужно научиться оперативно перебалансировать поток создания в зависимости от текущей ситуации. Спланировали работу персонала, оборудования и техники исходя из условий согласованной работы, начали работать, по мере нарастания дисбаланса в потоке из-за вариаций, запускаем процедуру его перепланирования… и так на постоянной основе. Тем самым, частым перепланированием потока мы постоянно перегруппировываем работу персонала, оборудования и техники таким образом, чтобы они работали максимально согласованно и слаженно. Это позволяет кардинальным образом снизить «четыре вида потерь» — запасы в сырье и материалах, запасы в персонале, запасы в оборудовании и технике, запасы во времени исполнения заказов.»
Звучит классно. Но если задаться вопросом «как именно это можно сделать?», то может оказаться, что идея является, во многом, эквивалентом идеи «станьте ёжиками» из известного анекдота.
Просто взгляните на один штык лопаты глубже
Спланировали работу персонала, оборудования и техники.
Работаем.
Дисбаланс.
Перепланировали работу персонала, оборудования и техники.
Работаем.
Перепланирование персонала
Стоп. Что делает персонал в новом перепланированном варианте? Ту же работу на другом месте или другую работу на том же месте? Если первое, то это возможно. Например, водитель одного маршрута автобуса перешёл на другой маршрут. Или один механик вышел на работу не в понедельник, а в предстоящую субботу, чтобы починить станок, который вывели из эксплуатации на выходные.
А если это второе? Другая работа на том же (или другом месте) — это что? Водитель автобуса пошел заниматься в субботу его ремонтом? Или ремонтник, которому нечего ремонтировать, стал за фрезерный станок и стал «давать план»? Это возможно?
Возможно, но при очень большом напряжении управленческого ресурса. Такие перепланирования предполагают более-менее гомогенную квалификацию персонала. Или, как минимум, наличие 3-4 профессий у каждого исполнителя. Причем не «абы каких», типа «умение подметать пол» или «навык покраски травы», а очень даже конкретных, нужных на данном типе производства. Если их нет — никакое перепланирование ресурсов не сделает из сварщиков сборщиков, а из электромонтёров токарей-фрезеровщиков.
Перепланирование оборудования
Ещё хуже обстоит дело с оборудованием. Как вы предполагаете перепланировать работу оборудования в случае вариативности спроса? Поменять режим работы? С пятидневки в две 8-часовые смены на трехдневку в одну 12-часовую смену, а потом в семидневку в три 8 часовые смены? Это еще как-то возможно (если вы сможете найти столько операторов станков и другого вспомогательного персонала на всё время изменений). Или попросить литейные машины пофрезеровать временно заготовки (только на период пикового спроса), ну или, например, на конвейер по разливу газированых напитков организовать процессы брожения легких алкогольных напитков, или, например, организовать доставку гранитных пород до склада временного хранения в ковшах экскаваторов, которые выгребают обломки гранита из карьера после взрывных работ.
Гомогенность оборудования, которая потребуется для такого «перепланирования» может оказаться еще менее достижимой, чем гомогенность навыков персонала.
Автор тоже пишет о сложности задачи:
«Но переход на такое динамичное управление бизнесом требует существенной перестройки организационной модели бизнеса, но это уже другая история.»
Но мне кажется, в «общем виде» такую задачу можно решить только на очень больших, и очень простых (малопередельных) производствах, у которых подавляющее большинство ресурсов уже универсальны или гомогенны.
Есть ли что-то, что автор «упускает из виду»
Да. Иначе видов потерь было бы не меньше, а может быть и даже больше.
Вот, например, дефекты. В четырех «европейских видах потерь» их нет. Игнорируем эти потери? Нельзя. Почему тогда Сергей забыл о них? Можно высказать гипотезу, что он не сталкивался с производствами, на которых доля внутреннего брака достигает 95% (бывает и такое), да даже 20-30%% внутреннего брака достаточно, чтобы озадачиться вопросом снижения такого рода потерь. Но их как бы нет.
Избыточная обработка, вызванная неэффективностью технологии. Т.е. когда мы используем какую-то плохую, малопригодную технологию, в то время, как есть более качественная, быстрая, эффективная. В мире четырех «европейских видов потерь» такого не бывает. Либо все технологии заведомо самые совершенные (не верю в такое), либо длительные периоды времени об этом никто не задумывается.
Движения людей, которые связаны не с желанием «заняться хоть чем-то», а плохой организацией рабочего пространства. Этого тоже нет в четырех «европейских видах потерь». Всё уже отлажено, отработано и систематизировано? Снова не верю.
Перемещения материалов, которые тоже не связаны с желанием «заняться хоть чем-то». Не будь этих потерь, предприятия обходились бы вовсе без транспортной техники — без кранов, погрузчиков, конвейеров, ричтраков и прочего. Но всё это есть на «среднестатистическом российском предприятии». Частично это последствия «избыточной обработки» в виде негодных технологий, частично — последствия избыточных запасов, а частично — «просто по привычке».
Ну и перепроизводство — оно тоже не только ради «чем-то заняться» возникает. Хотя часто является следствием технологий, запасов, режимов работы и так далее.
Второстепенность лишних видов потерь
И снова вопрос: а где те предприятия, на которых эти проблемы имеют «второстепенное значение»? Снова это крупные, немолодые, на неновых рынках, с высокой степенью монополизации.
Годится ли европейский набор потерь для наших предприятий? Наверное, для некоторых годится. Но я бы не стал ограничивать себя только этими четырьмя. Это, скорее, самые простые потери с точки зрения финансового учета, основанного на классической логике массового производства. И не всегда они самые значимые для бизнеса.
Так что выбирайте сами, какую типологию потерь использовать. Меня Сергей не переубедил.
Оригинал статьи «Четыре вида потерь».
Кому это может быть интересно
Кому это может быть интересно
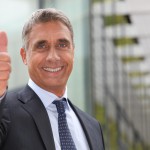
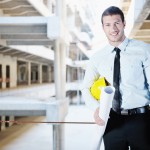
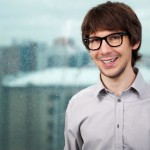
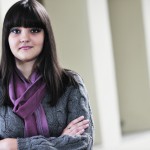
Узнать, кто эти люди…
Судя по книжке про ломку стереотипов, её авторы и раньше не понимали суть TPS. А судя по твоему, Валера, изложению, вообще путаются в основах. Если совсем коротко, то в теории движения материальных потоков есть базовое понятие «вариабельность». Понятно, что чем она выше, тем всё хуже, включая разбалансированность отдельных процессов. Так вот, вариабельность имеет смысл сокращать, а для этого нужно добраться до её источников. На Тойоте выделили 7 таких источников, назвали их «потерями» и придумали инструментарий устранения. Однако сократить вариабельность до нуля практически невозможно. Поэтому остаточную вариабельность нужно буферировать. Тут вообще не надо открывать Америку. Буферы бывают только трёх типов: запасов, мощности и времени. Причём хоть в Европе, хоть в Японии, хоть в Африке. Это как раз то, что указанный тобой автор ошибочно называет «четырьмя потерями» (персонал и оборудование, очевидно, это мощности). Действительно, буферирование связано с экономикой. Грубо говоря, чем больше размеры буферов, тем они дороже обходятся компании. Так что размеры буферов желательно сокращать. В этом смысле это потери для бизнеса. Но не для клиентов. Потому что, если две компании предлагают продукты с одинаковыми потребительскими свойствами и по одинаковой рыночной цене, то клиентам, вообще говоря, «по барабану», — больше или меньше затрат они при этом несут. Кстати, из трёх видов буферов самым предпочтительным считается мощность. И на Тойоте так делают, и в Европе.