Роль Сигео Синго в создании TPS, Производственной Системы Toyota, на мой взгляд несколько переоценена в России. Но для популяризации TPS, или бережливого производства, как мы его называем, Синго сделал очень много. И жаль, что на русском языке вышла только одна его книга, о быстрой переналадке.
Исправляя эту историческую ошибку, предлагаю вашему вниманию перевод третьей части книги Сигео Синго «Zero Quality Control: Source Unspection and Poka-yoke System».
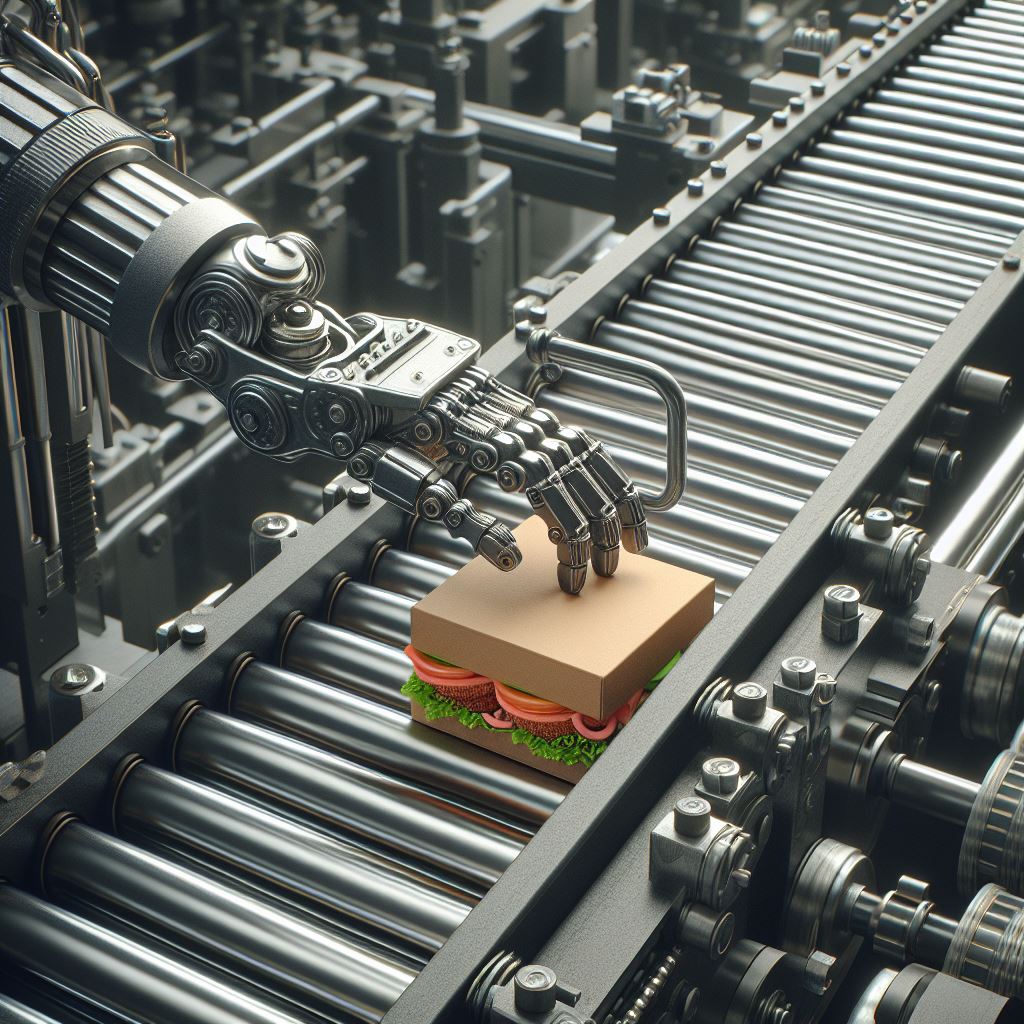
Часть 3. Инспектирование брака не сокращает количество дефектов
Увеличение количества инспекторов (количественное улучшение)
Во время одного из моих визитов директор завода A Industries пожаловался, что просто не может найти способ уменьшить количество дефектов.
Я просил: «Что ты пробовал сделать?»
Он рассказал мне, что инспектор в самом конце рассматриваемого процесса отделял хорошую продукцию от бракованной, но примерно 100 единиц из каждых 1000 были бракованными. Тогда директор завода распорядился увеличить число инспекторов. На следующий день количество бракованных единиц снизилось до 80, а на второй день оно упало до 60. Он почувствовал некоторое облегчение от того, что оказался на правильном пути, но на четвертый день количество бракованных единиц снова выросло, на этот раз до 120.
«Что мне, черт возьми, делать, чтобы устранить дефекты?» — спросил он меня.
Вот что я сказал директору завода:
«Два инспектора могут обнаружить дефекты, которые могут ускользнуть от одного инспектора, и использование двух инспекторов действительно может устранить такие упущения и удержать вас от попадания дефектных товаров в годные, которые вы отправляете клиентам.
Однако этот вопрос не имеет отношения к вопросу сокращения дефектов.
В любом случае, нет особого смысла проверять товар в конце процесса. Поскольку в ходе процесса возникают дефекты, всё, что вам нужно сделать, — это обнаружить эти дефекты. Добавлять проверяющих бессмысленно, потому что невозможно уменьшить количество дефектов без использования методов обработки, которые вообще предотвращают возникновение дефектов.
Из этого следует, что при обнаружении дефекта вы должны отправить информацию об этом назад, на предыдущий этап работы, чтобы можно было исправить процесс обработки.
В любом случае, это неизменный факт: обработка приводит к дефектам, и всё, что могут сделать проверки, — это выявить эти дефекты. Поэтому подходить к проблеме только на этапе проверки бессмысленно».
Проведение более качественных проверок (качественное улучшение)
Во время моего визита в компанию V Industries, производителя упаковочных материалов, руководитель инспекционного отдела, господин Вакабаяси, задал следующий вопрос.
Оказалось, что после того, как продукция была отправлена материнской компании, во время проверок, проводимых при получении продукции, иногда обнаруживались дефекты. Господин Вакабаяси был обеспокоен тем, что ему даже пришлось посетить головную компанию на острове Кюсю для повторных проверок.
«Почему», — спросил я его, — «как вы думаете, ваша материнская компания обнаруживает дефекты, когда принимает поставку вашей продукции? Я могу предположить две возможные причины. Либо ваша материнская компания обнаруживает дефекты, которые остались незамеченными на вашем заводе, либо она считает дефектными некоторые изделия, которые вы считаете удовлетворительными.
Похоже, вы осматриваете и ощупываете изделия, чтобы оценить внешний вид и твердость ваших упаковочных материалов. У вас есть образцы допустимых пределов?»
Я сказал ему, что у него должны быть такие образцы, и что кто-то из инспекционного отдела должен присутствовать при определении стандартов качества. Я также пожурил его, когда он признался, что, хотя руководитель технического отдела и побывал на указанном совещании, там не было никого из отдела контроля качества.
Он сразу предложил направить в головную компанию представителя отдела контроля качества для достижения соглашения по качеству и, в частности, по образцам допустимых пределов.
Его отдел затем мог принимать или не принимать продукцию на основе этих образцов, и это полностью устраняло дефекты, обнаруживаемые в материнской компании во время проверок поставок. Когда я ушел от него, он сказал мне, что его цель — сократить внутренние дефекты вдвое. Я пожелал ему удачи.
Когда на следующий месяц я посетил V Industries, г-н Вакабаяси показал мне статистику проверок и с гордостью объявил, что он достиг своей цели по сокращению внутренних дефектов. Мы поздравили друг друга с его достижением.
Впоследствии, во время осмотра завода, я заметил большое количество упаковочного материала № 2810 — продукта, который раньше вызывал проблемы — выброшенного в мусорные баки рядом с вулканизационным прессом. Я сказал оператору, что здесь, похоже, было много дефектов. Я спросил: «проблема была в сырье?»
«Нет», — ответил он, — «просто руководство в последнее время слишком суетится с этими проверками, поэтому мы выбрасываем все материалы, которые похожи на негодные».
В прошлом процент брака был высоким, поскольку все явно дефектные товары выбраковывались, а остальные отправлялись на проверку. Теперь выбрасывали все изделия, которые казались хотя бы немного странными, в том числе и вполне хорошие.
Несмотря на статистические данные, показывающие, что дефекты сократились вдвое, «абсолютный процент брака» на заводе не только не снизился, но увеличился. Встревоженный этим, я позвал господина Вакабаяси в цех и попросил его посмотреть, что происходит.
«Это полная чушь, когда вы радуетесь 50-процентному снижению статистического уровня брака», — сказал я ему. «Вы ничего не добились, если вы не снизили абсолютный процент брака на заводе».
В ответ на мои комментарии г-н Вакабаяси сразу же внес следующие улучшения:
- Вдоль передней части нескольких вулканизационных прессов был установлен общий конвейер.
- Если каждый пресс обрабатывал, скажем, четыре единицы упаковочного материала, конвейер немедленно переносил эти четыре детали вместе на следующий процесс. Раньше товары не передавались на следующую операцию до тех пор, пока не завершалась обработка всей партии.
- На следующем этапе «удаление заусенцев» устраняли неровности поверхности, и изделия немедленно направлялись на проверку.
- В процессе контроля продукция, прошедшая проверку, помещалась вместе с другими такими же предметами на вращающийся стол.
- При обнаружении дефекта оператор нажимал кнопку, и подозрительная операция останавливалась.
- Затем инспектор, руководитель операции и оператор проверяли штамп. После устранения причины дефекта, например, после удаления обрезков или шлифовки царапин на штампе, работа возобновлялась.
Таким образом, сообщение об обнаружении дефекта немедленно передавалось обратно на рассматриваемую операцию, и работу не возобновляли до тех пор, пока не принимали меры по предотвращению повторения дефекта.
Более того, методы работы изменили таким образом, чтобы в случае появления трещины в одном из четырех штампов, этот штамп нельзя было использовать.
В результате этих изменений абсолютный процент брака на заводе снизился до одной десятой от прежнего уровня, а также резко снизился процент выявления дефектов в ходе контроля.
Вот важнейший урок этого эпизода: не имеет значения, насколько тщательно проводились проверки, потому что дефекты возникают на этапе обработки, и все, что могут сделать проверки, — это обнаружить эти дефекты.
Приведенный выше пример показывает, что количество дефектов невозможно уменьшить только путем внесения улучшений на этапе проверки, хотя такие улучшения, конечно, могут устранить дефекты в поставляемом товаре.
Наиболее фундаментальной концепцией для уменьшения количество дефектов в производственной деятельности является признание того, что дефекты возникают в результате работы, и все, что могут сделать проверки, — это обнаружить эти дефекты. Нулевых дефектов никогда не удастся достичь, если забыть об этой концепции. Это жизненно важный момент, и его никогда нельзя переоценивать. Более того, идея, которую он выражает, является краеугольным камнем, на котором построена система нулевого контроля качества.
Где найти оригинал
На русском языке книга Синго не публиковалась. Англоязычную версию можно поискать, например, на Amazon.
Кому это может быть интересно
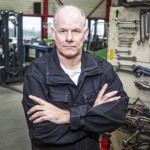
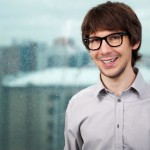
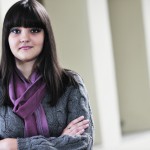
Узнать, кто эти люди…