Вытягивание предполагает запуск продукции по запросу клиента. Точнее после того, как он «изымет» из намеренно ограниченного запаса готовой продукции или незавершёнки какое-то количество изделий. То есть когда есть конкретный заказ. Идея производства на склад (в классическом виде) противоречит вытягиванию, т.к. это ведёт к нарушению правила об ограничении запасов.
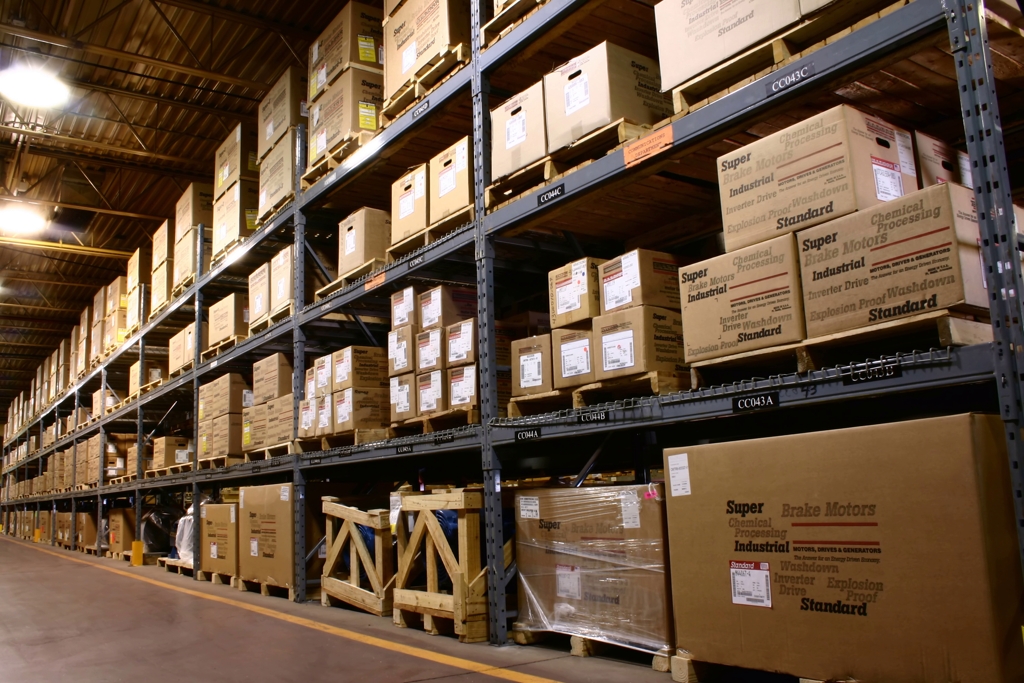
(Не забудьте прочитать начало серии, статью «Как перейти на вытягивание. Первые два вопроса«.)
Почему я сделал оговорку про «классический вид»? Потому что производство на супермаркет — это тоже «производство на склад», но там есть особенности, о которых напишу в одной из следующих частей.
Существует не так уж и много причин для того, чтобы производить продукцию «на склад» а не «на заказ». Попробуем разобраться с ними, чтобы вы представляли, что делать в вашем случае.
- Длинная переналадка. Размеры партий продукции, которые заказывает клиент, много меньше экономически обоснованных размеров партий производства.
- Срок изготовления. Цикл производства продукции заведомо дольше того срока, в течение которого клиент хочет получить свой заказ
- Ассортимент слишком большой. Периодичность пополнения запасов каждой единицы ассортимента значительно больше, чем частота, с которой клиенты заказываю эти изделия
- Непрерывное производство. Производство по технологическим причинам нельзя останавливать даже в том случае, когда в данный конкретный момент времени нет заказов.
- Наследие прошлого. Производство просто привыкло так работать, потому что «так было всегда». Других очевидных причин работать «на склад» на вскидку нет.
На вскидку на память не приходят другие причины. Но если вы знаете примеры, не охваченные этими пятью пунктами, обязательно напишите в комментариях или через контактную форму, вполне возможно, я что-то и забыл.
Длинная переналадка
Если клиенты заказывают по одному, два или три изделия, а производство не может выпускать их меньше, чем по пятьсот, очевидно, что без склада готовой продукции (СГП) не обойтись, т.к. иначе придётся выкидывать всё произведённое сверх заказа, пускать в переработку или делать с ним что-то ещё.
Что делать, если в вашем случае именно это является причиной использования схемы «производство на склад»?
Нужно предпринять два взаимонезависимых действия.
Во-первых, попытаться сократить размеры производимых партий настолько, насколько это возможно при ваших технологиях. Довольно часто, если речь идёт не о масштабном средесерийном или крупносерийном производстве, оказывается, что никто специально не анализировал возможности сокращения переналадок. Т.е. менеджеры и инженеры живут с тем, что есть. При это только за счет организационных изменений можно добиться сокращения времени переналадки на 30-40%%, что означает возможность соответствующим образом сократить размеры производственных партий.
В итоге даже если вам не удастся достичь тех размеров партий, которыми запрашивает продукцию клиент, вы всё равно сможете существенно сократить размеры партий и запасы на складе готовой продукции.
Во-вторых, попробуйте превратить СГП в склад незавершенного производства (СНЗП) выше по производственному потоку, т.е. на более ранних стадиях. Например, некоторые изделия можно хранить не в готовом виде, а в сборочных узлах, которые можно комплектовать уже после получения заказа клиента.
Что это даст? Вы избавитесь от некоторой части потерь, связанных с созданием дополнительной себестоимости для той продукции, которая в итоге не продастся и попадёт в утилизацию или на свалку: узлы по-отдельности имеют меньшую себестоимость, чем готовое изделие в сборе. Дополнительно вы освободите часть полезной производительности на сборочном участке.
Подробнее эту логику разберём в следующих частях этой серии статей.
Срок изготовления
Если производство продукции занимает месяц, а клиенту продукт нужен через неделю, как это бывает на некоторых рынках, вы не можете ждать заказов клиента для запуска производства, т.к. в этом случае вы будете опаздывать с исполнением каждого заказа. Поэтому разумной идеей в этой ситуации выглядит предложение держать некоторый запас готовой продукции на СГП и по мере её потребления пополнять этот запас запуском новых производственных партий.
Что с этим делать? Тоже предложу два направления действий.
- Сократить цикл производства методами бережливого производства, т.е. за счет сокращения потерь.
- Так же, как и в предыдущем случае, превратить СГП в СНЗП выше по производственному потоку.
Одна из основных целей большинства методов бережливого производства — устранение потерь в потоке создания ценности, а с потерями сокращается и цикл производства. Вряд ли вам удастся быстро сократить его до такого состояния, когда он станет меньше срока, который затребует клиент, но действия по сокращению цикла производства положительно повлияют и на уровень запасов, и на оборотный капитал, и на себестоимость продукции.
Возможно, вам удастся добиться нужных сроков по части ассортимента продукции. Это означает, что для этого ассортимента вы сможете применять принцип «производство на заказ» и избавиться от запасов готовой продукции. Для остальной продукции останется вторая тактика — перевод запасов с СГП на СНЗП.
Ассортимент слишком большой
Эта причина может быть связана с первой — длительностью переналадки, но может присутствовать и без неё. Когда у вас слишком большой ассортимент и нужно выпускать, например, 100 видов продукции в месяц, чтобы гарантировать запуска каждого продукта каждый месяц вам нужно каждый день запускать в производство партии трех позиций ассортимента, т.е. как минимум три партии.
При этом партия запуска каждого продукта должна быть рассчитана исходя из того, что в течение целого месяца продукция такого вида продукции больше не будет производиться, а это означает, что размер партии должен покрывать месячный спрос.
Если ассортимент вырастет до 150 видов изделий и мы не будем запускать больше трех партий разных видов продукции в день, то придётся уже рассчитывать на производство каждого продукта раз в полтора месяца и таким же образом рассчитывать запасы на СГП.
Причины могут лежать как в технических, так и в организационных аспектах производственного процесса.
Технические, скорее всего будут связаны опять же с переналадкой (первая причина) или с размерами транспортируемых партий как от поставщиков, так и внутри производства. Как ни странно, размеры транспортных партий тоже частично оправдываются переналадкой, но уже транспорта.
Соответственно, для решения этих проблем нужно заниматься сокращением времени переналадки, о чем я писал в разделе, посвящённом первой причине.
Организационные причины могут быть не столь очевидны, но они обычно легче поддаются корректировке. Вам необходимо проанализировать процесс планирования и запуска заказов в производство, чтобы ответить себе на вопрос: «если производство может делать что-то меньшими партиями, почему мы запускаем партии таких размеров? Кому в офисе/отделе продаж/плановом отделе/диспетчерском отделе/отделе закупок/экономических службах нужно, чтобы частота запуска партий была именно такой?»
Обычно помочь в анализе процесса помогает его описание, лучше всего в формате плавательных дорожек или кросс-функциональной диаграммы, обязательно с временной шкалой. По ней будет видно, где, что и почему тормозит течение потока.
Непрерывное производство
В случае непрерывного, недискретного производства, вам всегда где-то нужен склад для той продукции, которая «выпихивается» технологическим процессом с непрерывных переделов (этапов производства).
Предприятия, технологии которых описываются термином «непрерывное производство» можно разделить на два подтипа.
В первом подтипе все этапы производства непрерывны. Т.е. до самого момента отгрузки/отправки продукции клиенту мы имеем дело с непрерывным потоком продукции.
Примером может быть что-то типа электростанции или нефтеперерабатывающего завода, который отправляет свою продукцию потребителям по трубам.
Во втором подтипе часть этапов производства непрерывна, а остальные этапы имеют дело с дискретными продуктами, т.е. отделяемыми друг от друга.
Например, переработка молока заканчивается разливом готового молока в литровые пачки, которые можно поштучно, палетами или другими партиями передавать клиентам.
Другой пример — целлюлозо-бумажный комбинат. Часть технологии ЦБК непрерывна, вплоть до получения рулонов бумаги. Затем следует дискретная часть производства, где большой рулон бумаги нарезается на части — например, на листы формата А4 для офисной бумаги, которые комплектуются в пачки по 500 штук, упаковываются в коробки по пять пачек и дальше пакуются в палеты.
В первом случае вы и так имеете дело с вытягивающей системой, т.к. запасы сырья и полуфабрикатов в производственном процессе ограничены объемом емкостей и буферов хранения.
Во втором случае у вас есть вытягивающая часть — это непрерывная часть техпроцесса, и дискретная часть, работу которой можно построить как и в логике вытягивания, так и в логике выталкивания. Чаще всего её организуют так, чтобы все полуфабрикаты максимально быстро доводились бы до состояния готового продукта, который размещается на СГП.
Вот в этом конкретном случае снова можно говорить о том, чтобы переместить запасы с СГП на СНЗП.
Наследие прошлого
С одной стороны «наследие прошлого» — это не повод работать именно так, поэтому мне даже сам этот тип причин не пришёл в голову сразу. Я вспомнил о таком варианте только спустя несколько часов после того, как написал предыдущую часть статьи.
Но, с другой стороны, если задуматься, то оказывается, что очень многие предприятия работают именно так. «По привычке».
И если это ваш случай — поздравляю, вы в хорошей компании «старых добрых производственных предприятий», которые имеют в прошлом хорошую историю, известный бренд, и, вполне возможно, кучу проблем в настоящем.
«По привычке» можно заменить на «неосознанно». И тогда всё встаёт на свои места. Находясь внутри, мы часто не видим изменений, которые происходят с нашими компаниями. Меняются внешние условия, становится сложнее продавать, мы затягиваем пояса, но продолжаем работать. Пока кто-то снаружи не крикнет: «Эй, ребята, вы сейчас сваритесь, в этой кастрюле воду подогрели уже до 45 градусов!»
Если что-то с этим и можно сделать, то только через осознание. Нужно быстро собраться с мыслями, подтвердить себе, что производство действительно (по крайней мере в подавляющем большинстве случаев) работает на склад, и дальше срочно нужно определить основную причину, опираясь на предыдущие четыре версии.
Если верна одна из них — то и действовать нужно в соответствии с тем, что я рекомендовал выше.
Если не верна ни одна — это означает только то, что вы вполне легко можете перейти на производство под заказ и не волноваться больше о запасах на складе СГП. Не правда ли, было бы здорово?
Когда всё сложно
Что делать в том случае, когда часть ассортимента делается «под заказ», часть «на склад», при этом по разным причинам?
В принципе, всё очень просто и одновременно довольно сложно.
Простой ответ: разделите весь ассортимент на несколько соответствующих категорий продукции, и работайте с каждой категорией отдельно — каждая такая категория требует своей логики управления.
Почему сложно? Потому что если вы последуете этому простому совету, то «простая» логика планирования производства канет в Лету, останется с прошлым, а сложность вашего процесса планирования увеличится на один дополнительный критерий, «категория товара».
Получится, что что-то вы будете делать под заказ, что-то — на СНЗП, а что-то — на СГП. И в случае поступления заказа от клиента, который хочет «и того, и другого, и третьего» вам придётся для одних позиций заказывать сырьё у поставщика, потом, возможно спустя несколько дней, забирать полуфабрикаты с СНЗП под сборку других позиций заказа, а когда и то и другое приедет на СГП, доукомплектовывать их тем, что уже давно пылится на складе. И когда заказ уедет к клиенту, вам придется продолжить работать с ним — пополнять СНЗП и СГП. Плановикам тут будет где поработать засучив рукава.
Ну а продолжение плана перехода на вытягивание последует в третьей заметке на эту тему. Начало можно найти здесь.
Кому это может быть интересно
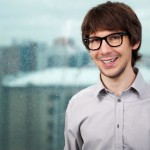
Основное узкое место, почему не останавливают оборудование это большие потери материала при чистке и времени при последующем запуске, а не потому что так делали всегда. Эпоха индустриализации оставила оборудование с высокой производительностью для крупных размеров партий. Увы, никто не задумывался раньше делать более производительное оборудование, но для малых партий. Как результат, в большинстве случаев требуется модернизация оборудования, либо использование только стабильного продукта для создания системы вытягивания.