Дискуссия в одной из Телеграм-групп подтолкнула задуматься над вопросом, который я вынес в заголовок. Один из участников спросил, каким должно быть оптимальное соотношение между временем переналадки и временем обработки партии между переналадками.
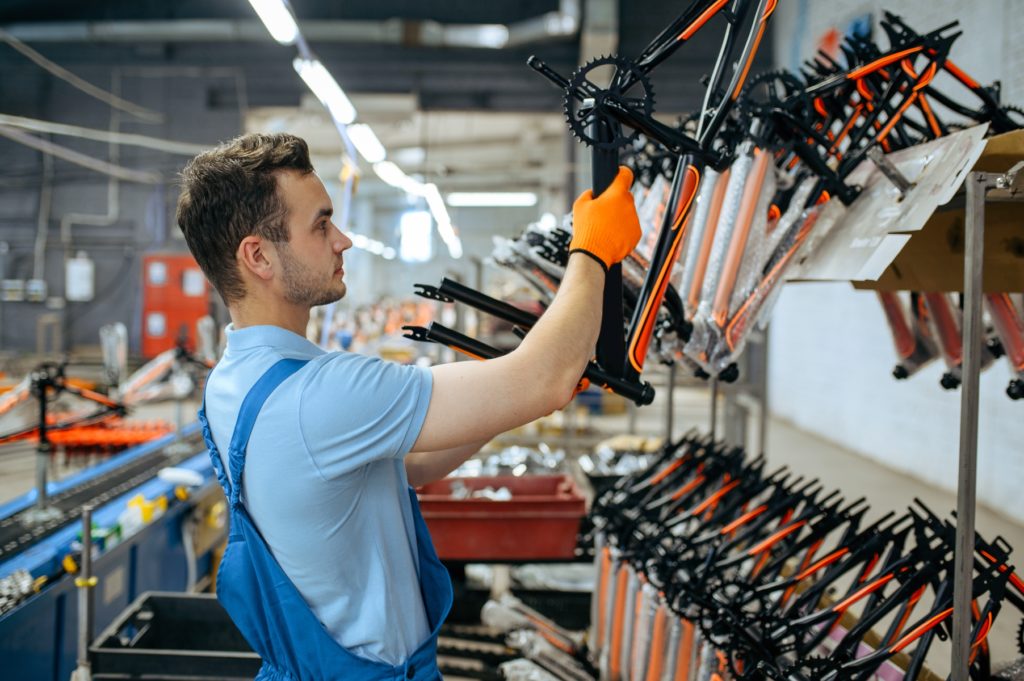
Время переналадки — константа или переменная?
Многое решает именно точка зрения на продолжительность переналадки. Если считать, что время переналадки детерменировано и тратить на переналадку меньше времени невозможно (если только не заставлять наладчиков бегать взад и вперёд с высунутыми языками и делать все операции как можно быстрее), то тогда можно только смириться с этим злом, съедающим производственное время, и пытаться минимизировать его за счёт увеличения размеров партий и сокращения частоты переналадок.
Если же вы вдруг признаете, что продолжительность переналадки не является константой и на неё можно воздействовать, не вынуждая наладчиков рисковать своим здоровьем и безопасностью, то тогда появляется возможность уменьшить время переналадок и делать их столько, сколько нужно, а не столько, сколько получается.
Правила управления количеством переналадок
Вопреки желанию уменьшить потери времени на переналадки и делать их как можно реже, для общего благосостояния всех сотрудников предприятия будет лучше, если переналадок будет достаточно много. Почему? Например, вы имеете возможность сделать две партии одного и того же продукта в течение недели или объединить их и сделать весь продукт одной партией. Как лучше?
Если не брать в рассмотрение ситуации, когда технологически для обеспечения одинакового качества лучше выдерживать большие размеры партий (например, при изготовлении настенных обоев или облицовочной плитки), то во всех иных случаях для предприятия выгоднее делать две переналадки и производить продукт двумя партиями, чем делать одну переналадку и выпускать продукт одной партией.
Почему? Плюс одной партии — экономия одной продолжительности переналадки. За это время можно произвести еще сколько-то изделий. Минус одной партии — нужно вдвое больше сырья и материалов, а под них до этого — денег, чтобы всё изготовить, а потом — нужно вдвое больше складских площадей, чтобы хранить все произведённое. К тому же всегда остаются риски порчи при хранении и устаревания готовой продукции, когда вы остаётесь один-на-один с неликвидом.
Правило 1. Задействуйте свободное время оборудования
Если у станка или линии есть простои, это означает, что можно совершенно безболезненно увеличить частоту переналадок. Добавить столько переналадок, чтобы они уместились в общую продолжительность простоев. Например, если за месяц набегает 10 часов простоев, а средняя переналадка занимает полтора часа, то теоретически можно безболезненно выполнить дополнительные 5-6 переналадок.
На что их использовать? На то, чтобы раздробить самые крупные партии и делать их «частями».
Может возникнуть вопрос целесообразности, если на других этапах те же самые изделия обрабатываются одной партией (по технологическим причинам или из-за высокой загрузки оборудования). Зачем делать лишнюю переналадку в этом случае? Но даже в этом случае предприятие получает выгоду за счет сокращения общих запасов незавершённого производства и, как следствие, увеличения средней скорости исполнения заказов. Подробности того, как возникает эта выгода, нужно рассматривать отдельно.
Недостатком увеличения количества переналадок будет увеличение потребления расходных материалов, необходимых для переналадки, увеличение трудозатрат наладчиков, снижение доступности оборудования.
Нужно ли занимать вообще всё свободное время оборудования? Скорее всего не стоит добиваться полной загрузки. Из теории очередей известно, чтоб для того, чтобы обеспечить максимальную загрузку станка, нужно увеличивать очереди ожидания.
Правило 2. Сокращайте время переналадки
Если оборудование не простаивает или, еще хуже, его не хватает, используйте SMED (single minute exchange of die, «замена штампов за несколько минут» или quick changeover, быструю переналадку) для сокращения времени переналадки.
Обратите внимание, что время может тратиться на «псевдо-переналадки», т.е. когда после некоторого простоя вы продолжаете выпускать ту же самую продукцию, но на некоторое время останавливаете производство.
Например, такие ситуации возникают при замене инструмента. Инструмент изнашивается и его нужно менять, хотя при этом продолжается производство того же самого продукта. Оборудование останавливается, инструмент меняют и запускают производственный процесс снова. Процесс замены инструмента — это такая «псевдо-переналадка» в упрощённой форме.
Другой случай «псевдо-переналадки» может возникать при доставке/загрузке/выгрузки очередной партии сырья. Если она меньше, чем то, что требуется для производства одной партии готовой продукции, то происходит тот же самый процесс. Оборудование останавливается, подвозится и загружается или выгружается и отвозится очередная партия сырья или готовых полуфабрикатов. После этого производство возобновляется. Это опять упрощенная версия переналадки.
Цикл работы по сокращению времени переналадки может занять от двух дней до нескольких недель. После этого у вас в производственном плане появится свободное время. Можно будет вернуться к Правилу 1.
Правило 3. Добавьте одну переналадку, чтобы продолжить совершенствование
Если всё идёт как надо, то есть простоев в работе ключевого оборудования нет и переналадок хватает, чтобы поддерживать текущий уровень спроса, то стоит подумать о будущем. Что будет, если спрос вырастет или изменится? Сможете ли вы обойтись текущим количеством переналадок? Хватит ли доступного времени для того, чтобы осуществить все переналадки, если потребуется увеличить их количество?
Конечно, ситуация комфортная и хочется ничего не менять. Но в будущем ситуация может измениться, а значит, нужно быть к этому готовыми.
Добавьте в план производства еще одну переналадку, разбив самую длинную партию на две части. Это потребует дополнительного времени и усилий. Теперь можно перейти к Правилу 2.
Краткая инструкция по определению количества переналадок
Вот эти три пункта родились в дискуссии в Телеграме:
- Если у вас остаётся свободное рабочее время на станке/линии/конвейере, в течение которого уже нечего производить, это означает, что нужно делать переналадку чаще.
- Когда свободного времени нет, а производство не справляется с исполнением заказов, не надо делать переналадку реже, надо делать переналадку короче, т.е. внедрять SMED.
- Если времени «ровно столько, сколько надо», значит в цикле планирования надо закладывать на одну переналадку больше. Например, в течение месяца, недели или смены, в зависимости от величины EPEх (every product every interval) или по-русски КПК (каждый продукт каждые…). Как следствие придётся делать переналадку короче.
Что делать дальше?
Если вам нужна помощь в организации быстрой переналадки — свяжитесь со мной. Есть два простых варианта и один сложный:
- Тренинг по быстрой переналадке. Один день с разбором конкретного примера с вашего производства
- Недельный проект по внедрению быстрой переналадки. Включает обучение по теме и большую практику решения проблем, связанных с конкретным примером.
- Полноценный проект по расшивке узких мест в производственной цепочке.
Совсем короткий обзор метода быстрой переналадки можно найти на моем канале на Youtube.com.
Кому это может быть интересно
Кому это может быть интересно
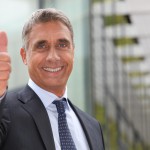
Кому это может быть интересно
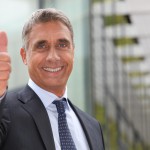
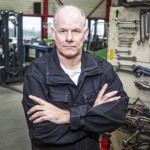
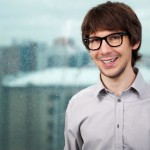
Узнать, кто эти люди…