Получил вот такой вопрос по почте от одного клиента:
«Я прочитал книгу «В.Е. Растимешин, Т.М. Куприянова Упорядочение. Путь к созданию качественного рабочего места. Практическое пособие»…. и у меня возникли сомнения по поводу правильности выбора участка внедрения TPM. Из книг я почерпнул информацию, что система 5С — подготовка к внедрению системы TPM на участке. Пятый шаг внедрения системы 5С является первым шагом внедрения системы TPM… Не получится ли у нас так, что по причине неготовности сотрудников к внедрению системы TPM мы просто не сможем завершить проект успешно?.. Не будет ли более правильным решением начать внедрение системы TPM на участке, где были проведены работы по стандартизации?»
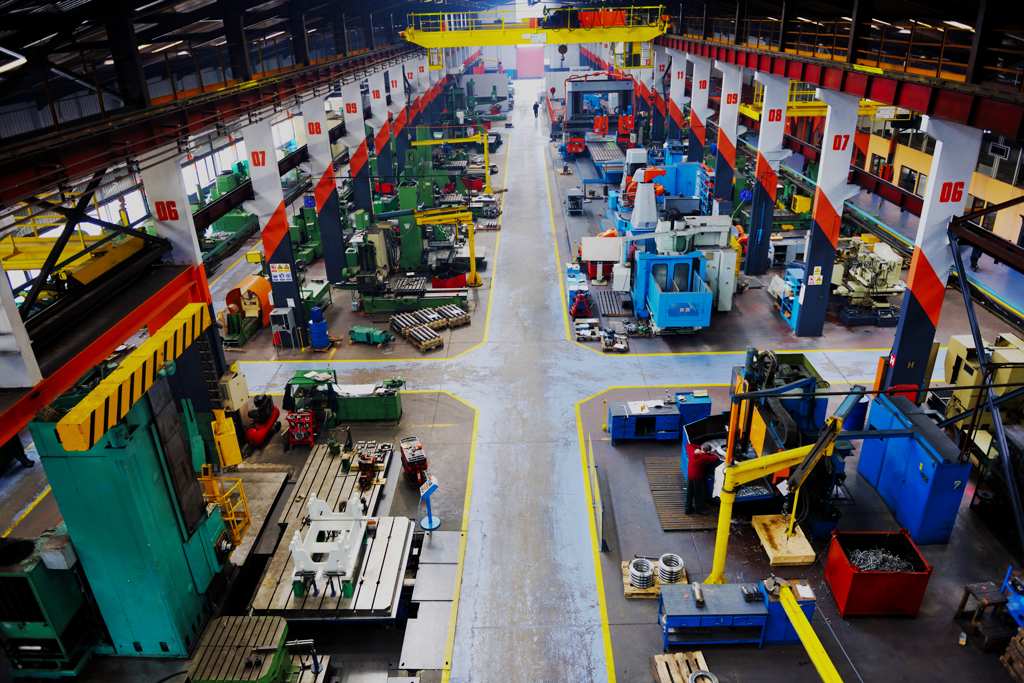
Я думаю, что ответ будет интересен многим читателям.
В моем опыте были разные способы внедрения TPM. В том числе и в формате, когда никаких стандартов и 5S в основе не было. Это «желательное», но не обязательное условие. Здесь, по моему мнению, стоит ориентироваться на текущее состояние дел и задачи, которые стоят перед производством и оборудованием. Если люди не привыкли к стандартам и на участке нет контрольных листов проверки оборудования, то как раз попытки разобраться, что не так с обслуживанием оборудования, и приведут к пониманию необходимости стандартов — мы выстраиваем систему и пытаемся выстроить все элементы лучшим образом. Если при этом видно, что проблемы связаны с ошибками в обслуживании, или с тем, что нет порядка в рабочей зоне, то попытка ответить на вопрос «что нужно сделать, чтобы устранить причины этих проблем» приведет к нужным нам ответам: надо поддерживать порядок на участке, нужно регулярно контролировать состояние оборудования, нужно…
Такой подход поможет работникам осознать потребность в порядке и осознанно этот порядок сформировать. Таким образом внедрение 5S и стандартов будет выполняться не по приказу сверху, исходя из «текущего состояния» и фотографий лучших практик, а исходя из той глобальной задачи, которую они будут решать. Это позволит избежать «перегибов», часто возникающих при внедрении 5S. Например, если нет проблем с хранением инструмента или оснастки, не надо специально покупать стенды, делать теневые шаблоны и так далее. Да, с помощью таких стендов и разметки мы упростим работу с инструментом, но если при этом главная проблема в другом, например в том, что замена форм на упаковочной линии выливается в головную проблему из-за износа оснастки, то мы получим эффект «игры в бирюльки» — люди будут думать «ага, нас заставляют гаечные ключи развешивать, вместо того, чтобы решить проблему, которая уже всех достала», и это точно не лучший способ вовлечения людей в процесс совершенствования.
В общем, как в присказке о том, что выроненные ключи надо искать в том месте, где потерял, а не там, где фонарь светит: если первоначально участок внедрения выбрали потому, что там больше всего проблем, либо потому, что на нем проще тренироваться, то лучше сохранить эту логику. В конце-концов, если через неделю-другую вы скажете «да, люди поняли, что им нужны стандарты, но мы хотим это сделать так, как у нас это принято» — ну, значит остальную деятельность по TPM можно на некоторое время приостановить, чтобы сфокусировать свои усилия на разработке нужных стандартов.
Зато люди будут точно знать — стандарты нужны не потому, что начальство требует, а потому, что без них добиться эффективной работы оборудования невозможно.
Еще раз повторю — в моей практике были примеры, когда мы работали с оборудованием несмотря на то, что 5S не было вообще, а были и примеры, когда внедрение этих двух инструментов велось в рамках одного направления работ, которое так и называлось «5S+TPM». Из первой категории могу упомянуть проект на заводе компании С. На второй год проекта мы делали пилотное внедрение TPM на трех участках, и параллельно развертывали 5S по всем цехам. За год по TPM была проделана работа только в рамках первого направления «Отдельные улучшения» (до автономного обслуживания мы даже не планировали добраться в силу непростой производственной культуры), а по 5S за этот же год проделали работы только в рамках первых двух шагов — «сортируй» и «создай порядок». Потребовалось бы несколько лет, чтобы внедрить на этом предприятии 5S до пятого шага включительно, но эффект от применения TPM мы получили уже за первый год — лишний вагон готовой продукции был весомым аргументом, подтверждающим правильность решения «не ждать 5S, а делать параллельно».
Кому это может быть интересно
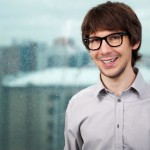
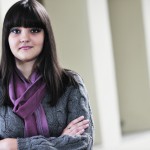
Узнать, кто эти люди…