На прошлой неделе обсуждал со слушателями курса по бережливому производству особенности применения лин в инструментальном цеху.
«Вчера нам весь день про Тойоту рассказывали. Так где Toyota, а где мы — для нас это вообще недостижимый космос!»
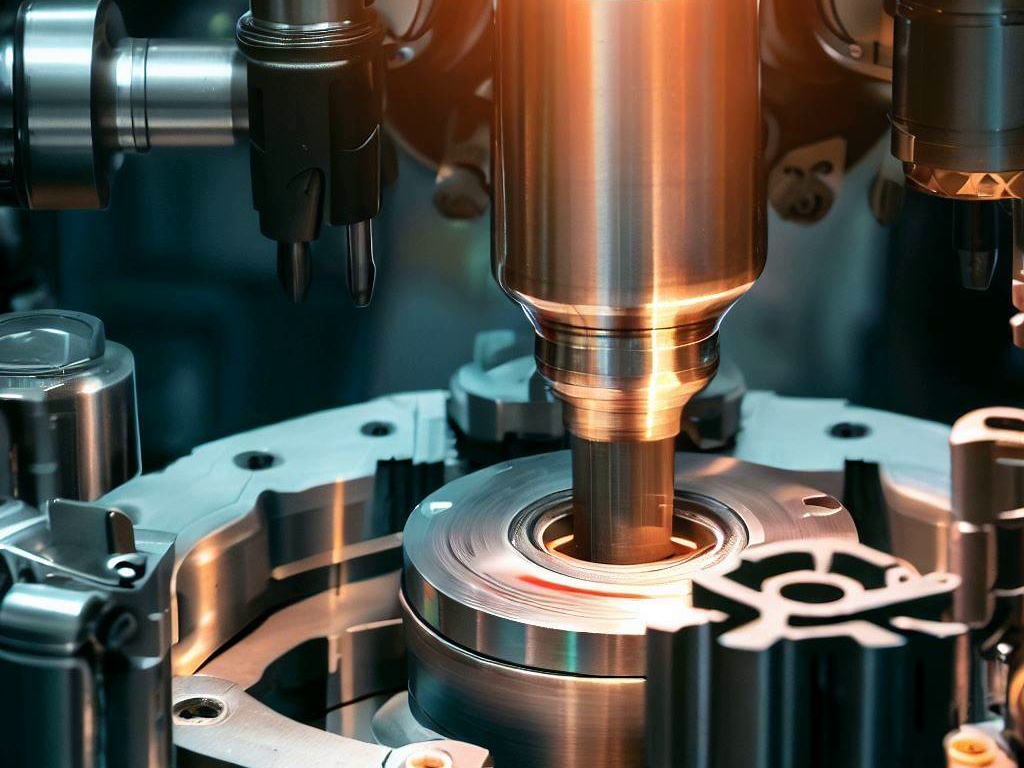
Не всё так плохо, на самом деле, хотя для того, чтобы получить от бережливого производства выгоду в штучном производстве инструмента, надо основательно поработать мозгами.
Один из примеров применения я нашёл, размышляя над давно завершённым проектом, буквально за пару дней до этой дискуссии. Речь идёт о переналадке станка с ЧПУ для изготовления штучных деталей — инструмента или частей оснастки.
Процесс, как он есть сейчас
Оператор станка с ЧПУ устанавливает на станке заготовку. Чтобы вся программа отработала безошибочно, нужно правильно спозиционировать заготовку относительно плоскостей, в которых движется инструмент. Заготовку устанавливают с помощью фиксаторов, установленных в направляющие на опорной плите станка. Это занимает примерно полчаса. Потом оператор выбирает в памяти станка нужную программу обработки, закрывает рабочую зону, запускает станок и минут десять-пятнадцать ждёт. Потом снимает готовую деталь и дальше начинает всё сначала.
Полчаса он устанавливает заготовку, пятнадцать минут станок работает. Замену инструмента станок делает сам, с этим всё в порядке. А вот установка детали — это, по сути, часть переналадки, которая занимает очень много времени. Что делать?
Процесс, как он должен быть
Пока станок работает над предыдущей деталью, оператор станка с ЧПУ устанавливает заготовку не на опорной плите станка (она занята предыдущей деталью, работа еще не завершена), а на опорной подставке. Чтобы программа отработала безошибочно, нужно правильно спозиционировать заготовку относительно плоскостей, в которых будет двигаться инструмент.
Для этого оператор использует отдельную установочную зону, в которой может спозиционировать деталь относительно плоскостей опорной подставки. Заготовку устанавливают на ней с помощью фиксаторов. Это занимает примерно полчаса. Потом опорную подставку оператор установливает одним движением в направляющие на опорной плите станка. Далее оператор корректирует положение точки начала координат.
Потом оператор выбирает в памяти станка нужную программу обработки, закрывает рабочую зону, запускает станок и начинает на другой опорной подставке устанавливать следующую заготовку. Потом снимает готовую деталь и дальше начинает всё сначала.
Процесс, каким он должен будет стать в перспективе
При наличии двух сменных опорных подставок, которые единственным образом можно установить на опорной плите станка, в таком сценарии экономится до 15 минут на переналадке заготовок. Если покопаться в процедуре дальше и найти способы быстрого позиционирования заготовки на опорной подставке, то это время станет меньше продолжительности обработки, и тогда станок не будет простаивать вообще. Пока он будет делать предыдущую деталь, оператор будет успевать установить на опорную подставку следующую деталь. Как только станок остановится, завершит свою программу, оператор меняет местами две опорные подставки, запускает станок, снимает готовую деталь и снова ставит на её место новую заготовку.
Однодневный семинар по быстрой переналадке или короткий проект внедрения быстрой переналадки можно заказать в лин-магазине.
Кому это может быть интересно
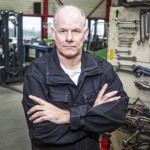
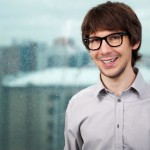
Узнать, кто эти люди…
Технология нулевых точек ( системы быстрого позиционирования) от Shunk и Erowa — коллегам в помощь